What is Six Sigma and Why is it Six Sigma?
(Six Sigma Meaning & Why 6 Sigma?)
Six Sigma is a practical strategy designed to enhance the quality of work in a business. It's like a helpful recipe aimed at identifying and eliminating flaws and reducing inconsistency in manufacturing or other processes in a company. Born within Motorola's thirst for flawless operations in the 1980s, it has since grown into a universally adopted tool helping companies such as General Electric and Amazon achieve exceptional efficiency and customer satisfaction. A peek into any of these successful businesses will reveal the remarkable power of Six Sigma, shaping the steps to their daily operations. Just imagine flicking on your phone without a hitch; that's Six Sigma at work.
Six Sigma is a data-driven methodology that aims to improve processes by identifying and eliminating defects or variations, ultimately striving for near-perfect quality with only 3.4 defects per million opportunities. It provides organizations with a structured approach to problem-solving and continuous improvement, leading to enhanced customer satisfaction and reduced operational costs.
What is Six Sigma?
At its core, Six Sigma is a structured, data-driven methodology seeking to enhance the quality of process outputs by minimizing variability and eliminating defects. Simply put,
Six Sigma is akin to having a quality control superhero that identifies and fixes any production or service delivery issues.
Picture this: In a manufacturing facility, there's a steady flow of products being made, each needing to meet a certain quality standard. However, tiny variations persist in the production process. Six Sigma steps in to analyze these variations and reduce them to virtually zero so that every product meets the desired standard.
The Quest for Near-Perfection
The ultimate goal of Six Sigma is near-perfection—how close? A failure rate of only 0.00034%. This translates to delivering near-perfect goods and services with just 3.4 defects per million opportunities. It may sound almost impossible, yet it's about striving for excellence and surpassing expectations.
To clarify further, an "opportunity" refers to the chance for a defect within a process. For instance, in manufacturing, an opportunity could be a specific step in the assembly line where a defect could potentially occur.
This relentless pursuit of perfection has captivated major players across various industries.
Companies like General Electric, Toyota, and Amazon have integrated Six Sigma into their business strategies with remarkable results. It has become a trusted methodology not only in manufacturing but also in healthcare, finance, and other service industries.
Having uncovered the essence of Six Sigma and its relentless pursuit of perfection, let's delve deeper into how it achieves these ambitious goals through its methodologies and principles.
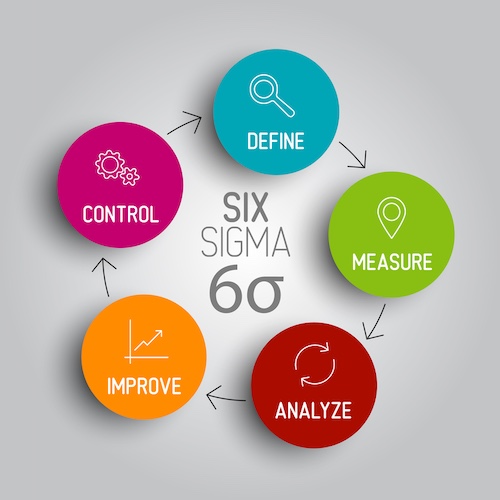
Six Sigma Meaning
The Origin of Six Sigma
Six Sigma traces its origins back to 1986 when it was crafted by Bill Smith, an engineer at Motorola. At the time, Motorola was striving for operational excellence and sought a robust method to achieve near-perfection in its processes. This pursuit led to the birth of the Six Sigma methodology, which aimed at minimizing variation and defects in production and business processes.
Motorola's pursuit of quality improvement through statistical methods laid the foundation for what would become a global phenomenon. The initial focus was on reducing errors and defects in manufacturing processes, leading to higher customer satisfaction and lower costs. It wasn't long before other industry giants took notice of Motorola's success with Six Sigma and started adopting it for their own operations.
In the early 1990s, General Electric widely popularized and implemented Six Sigma under the leadership of Jack Welch, who recognized its potential for transforming business practices and driving exceptional performance. GE's commitment to Six Sigma played a pivotal role in propelling the methodology into the mainstream, showcasing tangible results in improved quality, efficiency, and profitability.
The impact of Six Sigma extended beyond manufacturing, finding application in diverse sectors such as healthcare, finance, and service industries. Toyota integrated Six Sigma principles into its renowned Toyota Production System, leveraging statistical methodologies to enhance efficiency and minimize waste. Similarly, e-commerce titan Amazon harnessed Six Sigma to optimize operational processes and deliver consistent customer experiences at scale.
For instance, General Electric's implementation of Six Sigma yielded substantial benefits across its business units. The company found that even a small reduction in defects could result in significant cost savings while simultaneously enhancing product quality. Toyota's embrace of Six Sigma enabled precision engineering and leaner operations, contributing to its leadership in the automotive industry.
The journey of Six Sigma from its inception at Motorola to widespread adoption by industry leaders reflects its remarkable impact on process improvement and organizational success.
The Focus and Benefits of Six Sigma
The primary aim of Six Sigma is to ensure that an organization’s processes are as close to perfect as possible, delivering goods and services with utmost precision. It strives to minimize defects and variations in these processes, working towards flawless quality by eliminating potential issues or errors. But why is this focus of paramount importance?
Well, consider this - when you receive a product or service that meets your expectations without any faults or delays, how does it make you feel? Happy, satisfied, and likely to come back for more, right? That's the value of addressing defects and variations through Six Sigma - heightened customer satisfaction.
By obsessively focusing on reducing defects and variations, organizations can increase customer loyalty while also enhancing overall efficiency in their operations. It’s like aiming for a perfect bullseye every time.
Furthermore, by streamlining their processes and minimizing errors, companies can expect significant benefits. For instance:
Reduced Costs | Improved Quality | Increased Profitability |
By identifying and mitigating process inefficiencies, companies can eliminate unnecessary expenses associated with errors and defects. | A natural outcome of reduced defects is an increase in the overall quality of products or services. | As a direct result of improved quality and reduced costs, companies stand to see a significant increase in profitability. |
Imagine a scenario where a manufacturing company implements Six Sigma methodology to identify a particular machine on the assembly line causing production defects. By identifying and fixing this issue, they not only eliminate all defects from their produced goods but also reduce their production time by 50%, thus making significant cost savings.
That story is a testament to how Six Sigma methodology can truly transform an organization's productivity. In essence, it’s about identifying key areas where improvements can be made to unlock higher efficiency and cost-savings – ultimately enhancing the company’s competitive position in the market.
With a clear understanding of the power behind Six Sigma's focus and the benefits it delivers, we can now delve into its methodologies and tangible implementation strategies.
What is Sigma and Six Sigma in Statistics?
Mean is the arithmetic average of a process data set.
Central tendency is the tendency of data to be around this mean.
Standard Deviation (also known as Sigma or σ) determines the spread around this mean/central tendency.
The more number of standard deviations between process average and acceptable process limits fits, the less likely that the process performs beyond the acceptable process limits, and it causes a defect. This is the reason why a 6σ (Six Sigma) process performs better than 1σ, 2σ, 3σ, 4σ, 5σ processes.
Obviously 7 or more σ processes are even better than a 6σ (Six Sigma) process, and yet throughout the evaluation and history of Six Sigma process, the practitioners gained the belief that a 6σ process is good enough to be reliable in almost all major situations except some systems whose defects can cause unrepairable consequences.
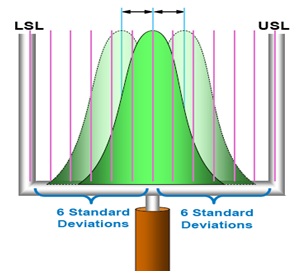
Six Sigma stands for 6 standard deviations (6σ) between avarage and acceptable limits
LSL and USL stand for “Lower Specification Limit” and “Upper Specification Limit” respectively. Specification Limits are derived from the customer requirements, and they specify the minimum and maximum acceptable limits of a process.
For instance in a car manufacturing system the desired average length (Mean length) of car door can be 1.37185 meter. In order to smoothly assemble the door into the car, LSL can be 1.37179 meter, and USL can be 1.37191 meter. To reach a 6σ quality level in such a process, the standard deviation of car door length must be at most 0.00001 meter around the mean length.
Sigma is also the capability of the process to produce defect free work. Higher the capability, lower the defects.
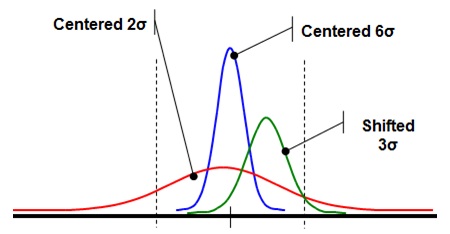
Processes in various Sigma Levels
In the above figure, the red curve indicates a 2σ level of performance where we observe that its peak is very low (fewer outputs are around the desired average) and the variation is from extreme left to extreme right of the figure. If the process improves from 2σ to 3σ (green curve), you will observe that the process variation reduces and the process has a larger peak (more outputs are around the desired average, but a different average than red curve). As the process performance increases from 3σ to 6σ (blue curve), the process becomes centered between the upper and lower specification limits and does not have much variation. Here with blue curve the majority of process outputs are around the desired average. This is why it is good and it causes less defects beyond the lower and upper specification limits.
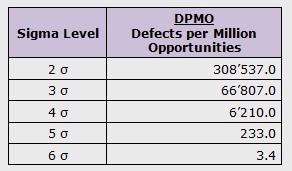
Sigma Level vs DPMO Defects per Million Opportunities
In the above table, you will observe that as the Sigma level increase the Defects decrease. For example, for a 2σ process the Defects are as high as 308,537 in one million opportunities. Similarly, for a 6σ process the Defects is as low as 3.4 in one million opportunities. The 2σ performance level will have more defects than a system in 6σ performance level as the standard deviation for a 2σ process is much larger than the standard deviation for a 6σ process.
Can we have any process which has 6σ level of performance?
The answer is yes. Pharmaceutical Companies, Airline Manufacturing Organizations, Automobile Manufacturers, among others are bound to work at a sigma level which is either 6σ or more than that. If they are not able to perform at this efficiency, the organization cannot exist. Think about it, you are in the air, 5000 feet above the ground, flying in a Boeing 777 Aircraft and suddenly a nut-bolt in the wing of the plane loosens (probably due to manufacturing defect) making it difficult for the pilot to steer the flight! This is the only reason why defects are not welcome and organizations try to achieve higher Sigma levels.
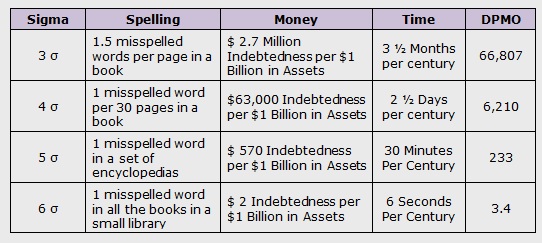
Six Sigma vs DPMO Examples
In the above examples,
- Sigma indicates the Sigma level.
- Spelling indicates the total spelling errors.
- Money indicates the amount of fine/indebtedness that can occur due to the misspellings.
- Time indicates the total time it takes to correct those misspellings.
- DPMO indicates the total Defects in One Million Opportunities.
We can clearly observe that as the Sigma Level increase, the defects (misspellings) decrease, the indebtedness reduce and the time for rework also reduces, thus it reduces the DPMO-Defects per Million Opportunities.
Six Sigma's Impact on Quality and Efficiency
Implementing Six Sigma methodologies is akin to committing to a relentless pursuit of perfection in the products or services a company offers. This involves a comprehensive approach focused on minimizing defects, reducing variation, and achieving consistent quality. By utilizing statistical analysis, companies can uncover the root causes of problems, whether it's an issue with production output or a flaw in service delivery.
Six Sigma tools allow organizations to measure and analyze their processes in great detail, pinpointing areas where errors occur and identifying variations that can impact product or service quality. Statistical methods such as control charts, process capability analysis, and regression analysis serve as the investigative tools that shine a light on where improvements are needed.
The impact of Six Sigma on a company's overall performance can be profound, leading to significant cost savings—sometimes in the millions of dollars—due to reduced errors and enhanced efficiency. When defects are minimized, and variation is reduced, companies move closer to delivering near-perfect goods and services with only 3.4 defects per million opportunities—the precision that customers demand and what sets them apart from competitors in terms of delivering unparalleled quality.
Toyota exemplifies the rewards of implementing Six Sigma methodologies. Through its commitment to continuous improvement and efficient processes, Toyota has set new industry standards for vehicle manufacturing by significantly reducing defects while maintaining high-quality standards.
In essence, Six Sigma's impact is far-reaching, touching every aspect of the production or service delivery process. From streamlining operations to enhancing customer satisfaction, the principles of Six Sigma create an environment focused on excellence and continual improvement. Companies implementing Six Sigma not only build better products or deliver more efficient services but also cultivate a culture that values quality, efficiency, and innovation—an environment where problems are addressed through data-driven solutions.
Six Sigma's emphasis on analytical problem-solving alongside data-driven solutions brings about noticeable changes in overall quality and results in significant process optimization and resource utilization.
Principles and Techniques: The DMAIC Approach
The DMAIC approach is at the heart of Six Sigma, providing a structured path for improving processes and achieving tangible results. Let's break down the five key phases of DMAIC, defining each step along the way.
Define
In this first phase, it's essential to clearly outline the problem or opportunity for improvement. This involves understanding the current state of the process, identifying customer requirements, and setting specific and measurable goals for improvement. The "define" step is all about laying a solid foundation by establishing what needs to be achieved and understanding the scope of the project.
Measure
Once the problem has been defined, it's time to gather data and measure the current performance of the process. This phase involves collecting relevant information, assessing process capability, and identifying critical factors that contribute to variation. Measurement is crucial in providing an objective understanding of the process's current state and highlighting areas for improvement.
Analyzing data during the "measure" phase helps in quantifying process performance and provides a baseline against which future improvements can be evaluated. This phase relies heavily on statistical analysis to provide an accurate representation of the process performance.
Analyze
With a wealth of data in hand, the next step is to interpret and analyze that data to identify root causes and factors contributing to process variation. The goal is to uncover insights and patterns that reveal why the process behaves the way it does. By drilling down into the data, teams can gain a deep understanding of the root causes behind inefficiencies or defects within the process.
By diving deep into data analysis, teams can gain valuable insights into where problems lie within a process. An iterative approach to analysis is often necessary as new information may come to light, allowing for a more comprehensive understanding of the issues at hand.
Improve
Armed with a thorough analysis, it's time to develop and implement solutions aimed at addressing identified issues. The "improve" phase involves generating ideas, testing potential solutions, and implementing changes that target root causes of variation. These improvements are implemented in a controlled manner to ensure they produce sustainable results.
Control
The final phase of DMAIC focuses on establishing controls to sustain the gains made during the improvement phase. This involves developing standard operating procedures, setting up monitoring systems to track process performance, and instituting measures to prevent regression. The aim is to embed changes within the organization's culture and ensure continuous improvement over the long term.
Each phase of DMAIC builds upon the last, creating a structured approach for analyzing processes, identifying areas for improvement, implementing changes, and sustaining those improvements over time. With DMAIC as a framework, organizations can systematically enhance their processes and achieve significant performance gains while aiming for near-perfection in their operations.
The practical application of these principles is what makes Six Sigma such a powerful methodology for driving continuous improvement within organizations across various industries.
Now let's move on to explore how businesses successfully implement the Six Sigma strategy in their operations.
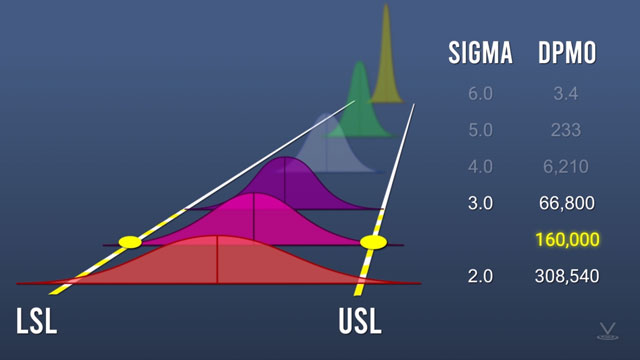
Why is it called Six Sigma?
Implementing the Six Sigma Strategy
So, you've made the decision to introduce Six Sigma into your organization. This is where things get really intriguing. We're not just talking about a new tool or program; we're discussing a transformation in how your organization operates, thinks, and even feels.
The first step in implementing Six Sigma is ensuring that everyone comprehends its fundamental principles and why it's crucial. This involves providing training and resources for employees at all levels, from top management down. It's imperative that everyone understands the basic concepts of Six Sigma so they can actively participate in improvement projects and support the implementation process.
To illustrate, consider a scenario where your organization has committed to a major project to reduce defects in a critical product line. For this initiative to succeed, every individual involved must grasp how Six Sigma operates to contribute effectively.
Apart from educating everyone about Six Sigma, another critical step is establishing clear metrics to measure progress. You need to determine if you are on the right track or not, and well-defined metrics help you achieve this. These measurements will enable you to comprehend how effective your processes are and identify areas for improvement.
It's analogous to driving—how do you know if you're making progress if you don't have a speedometer or a map?
When it comes to integrating Six Sigma into an organization's culture and operations, aligning the strategy with overall business objectives is crucial – ensuring everyone pulls in the same direction and that resources are allocated effectively without diluting their focus on organizational goals.
Implementing Six Sigma isn't just about adopting a new set of tools; it's about instilling a culture of continuous improvement within an organization. The journey may be challenging, but the rewards in terms of efficiency and quality can be truly transformative.
Frequently Asked Questions About Six Sigma
Are there any notable success stories or case studies related to six sigma implementation?
Answer: Yes, there are several notable success stories and case studies related to the implementation of Six Sigma. For example, General Electric (GE) implemented Six Sigma in the late 1990s, resulting in significant cost savings and improved efficiency. By 2001, GE had reported $2 billion in savings as a direct result of implementing Six Sigma. Additionally, Motorola successfully applied Six Sigma principles and achieved annual savings of over $16 billion. These success stories demonstrate the effectiveness of Six Sigma in driving process improvement and financial results.
What is the history and origin of the term "six sigma"?
Answer: The term "six sigma" was first coined by Motorola in the late 1980s to describe their approach to process improvement aiming for near-perfection by reducing defects. Inspired by statistical quality control methods, Motorola sought to achieve a six standard deviation variation from the mean, referred to as "six sigma," in order to achieve exceptional quality levels. Since then, the concept has been widely adopted in various industries, including manufacturing and service sectors, resulting in significant improvements in efficiency and customer satisfaction.
How has six sigma evolved over time and what are its key principles?
Answer: Six Sigma has evolved over time to become a comprehensive approach for process improvement. Initially developed by Motorola in the 1980s, it gained popularity in the 1990s and has since been adopted by various industries. The key principles of Six Sigma include customer focus, data-driven decision making, process understanding and control, and continual improvement. It aims to reduce defects and improve efficiency by statistically analyzing data to identify root causes and implementing systematic changes. According to a study by McKinsey, companies that successfully implement Six Sigma achieve significant cost savings and improvements in quality performance.
What industries or sectors commonly implement six sigma methodologies?
Answer: Six Sigma methodologies are commonly implemented in various industries, including manufacturing, healthcare, finance, and telecommunications. In manufacturing, companies such as Motorola and GE have reported significant improvements in quality and productivity through Six Sigma implementation. In healthcare, organizations like Mayo Clinic have seen reduced medical errors and improved patient outcomes using these techniques. Similarly, financial institutions like Bank of America have realized cost savings and improved customer satisfaction by streamlining processes using Six Sigma. According to a study by International Six Sigma Institute, the top industries implementing Six Sigma include manufacturing (38%), healthcare (21%), and finance (16%).
How can individuals or organizations benefit from understanding and applying the concepts of six sigma?
Answer: Understanding and applying the concepts of Six Sigma can bring numerous benefits to individuals and organizations. Firstly, it enhances quality control by minimizing defects and errors, leading to improved customer satisfaction. Secondly, it streamlines processes, reducing costs and increasing efficiency. Thirdly, it promotes a culture of continuous improvement, fostering innovation and adaptability in today's rapidly changing business environment. According to a study by International Six Sigma Institute, companies implementing Six Sigma achieved an average cost savings of $174,000 per project and an increase in customer satisfaction by 23%.
What is Sigma in Six Sigma?
Answer: Sigma in Six Sigma refers to standard deviations from the mean in a statistical distribution. It is a measure of variability and is used to quantify the performance of a process. The goal of Six Sigma is to achieve a level of performance where the process produces no more than 3.4 defects per million opportunities. The term "Sigma" is central to the methodology, and achieving higher Sigma levels indicates a more precise and reliable process. Six Sigma methodology involves trained individuals known as "belts," ranging from yellow belts for basic understanding to black belts for advanced expertise, who apply statistical tools and knowledge to improve various aspects of a process, from design to execution. By focusing on reducing variation and defects, Six Sigma aims to enhance overall efficiency and quality, involving people at all levels of an organization in continuous improvement efforts.
What is Sigma in Statistics?
Answer: Sigma in statistics is a symbol representing standard deviation, a measure of the dispersion of data points in a distribution. In the context of Six Sigma, a methodology widely applied in project management and process improvement around the world, Sigma levels are used to assess and enhance the performance of processes. Practitioners, often organized into teams, use statistical tools and techniques to analyze and optimize processes, aiming to achieve a higher Sigma level, indicative of greater precision and reduced variability. Certification programs, such as Six Sigma, provide practitioners with a structured model for implementing statistical practices in project management. These certified individuals, known as belts, collaborate with stakeholders to ensure that statistical principles are applied effectively, contributing to the success of projects and continuous improvement within organizations.
What would mean going from a 2 Sigma Process to a 6 Sigma Process?
Answer: Going from a 2 Sigma process to a 6 Sigma process signifies a significant improvement in quality management and operational efficiency. In the realm of Six Sigma methodology, Sigma levels represent the standard deviations from the mean, with higher Sigma levels indicating lower variation and better performance. Moving from 2 Sigma to 6 Sigma implies a substantial reduction in defects, from a relatively error-prone process to an exceptionally high-quality one. Achieving this leap involves a dedicated team practicing rigorous Six Sigma methodologies, including identifying and addressing root causes of variability. The term "Sigma," rooted in Greek mathematics, symbolizes the statistical precision and excellence sought in the pursuit of continuous improvement and optimal process performance.
What is Lean Six Sigma?
Answer: Lean Six Sigma is a comprehensive business strategy and practice that integrates the principles of Lean and Six Sigma methodologies. Lean focuses on the elimination of waste and streamlining processes, while Six Sigma emphasizes defect reduction and achieving a high level of process efficiency. Lean Six Sigma combines these approaches to address both speed and quality, incorporating performance metrics and root cause analysis to drive continuous improvement. It goes beyond a mere set of tools and becomes ingrained in the organization's culture, encouraging a systematic and data-driven approach to problem-solving. It's important to note that Six Sigma is synonymous with Lean Six Sigma, as the "Sigma" concept in Six Sigma is derived from the Lean Movement, underlining the integration of both methodologies for achieving optimal business performance.
Why Six Sigma is called Six Sigma?
Answer: Six Sigma is named after the statistical concept of standard deviation, represented by the Greek letter sigma (σ). The term "Six Sigma" signifies a level of performance where a process produces only 3.4 defects per million opportunities, aiming for an extremely high degree of accuracy and efficiency. The different belts in Six Sigma, such as yellow belt, green belt, and black belt, symbolize various levels of expertise and roles within the organizational culture. Individuals undergo Six Sigma courses to gain the knowledge and tools necessary for process improvement and change. For example, a yellow belt might have a foundational understanding, a green belt is equipped for intermediate-level projects, while a black belt holds advanced expertise and leads significant improvement initiatives. The numerical designation underscores the rigorous quality standards Six Sigma strives to achieve, emphasizing a commitment to minimizing defects and promoting a culture of continuous improvement within an organization.
What are USL and LSL in Six Sigma?
Answer: In Six Sigma, USL (Upper Specification Limit) and LSL (Lower Specification Limit) are critical terms related to process control and ensuring product quality. These limits define the acceptable range of variation for a particular process or its outputs. The purpose of establishing USL and LSL is to identify the upper and lower boundaries within which the inputs or parts produced by a process should fall to meet customer requirements. By setting these limits, Six Sigma practitioners can monitor and control the process to ensure that it consistently delivers outputs within the specified range. Any deviation beyond these limits may indicate a potential issue in the process, prompting corrective actions to maintain product quality and align with customer expectations. The careful management of USL and LSL is essential for achieving the desired level of performance and minimizing defects in the production of parts or services.
Why 6 Sigma but not 7 Sigma?
Answer: Six Sigma, as opposed to 7 Sigma, is a strategic choice that balances precision with practicality in process improvement. While achieving a higher number of standard deviations (Sigmas) theoretically implies a more precise and efficient process, the decision to stick with Six Sigma is rooted in practical considerations. The cost and effort involved in reaching 7 Sigma levels may outweigh the tangible benefits, as the incremental improvements become increasingly challenging. Moreover, for most industries, meeting customer expectations and maintaining a robust bottom line can be effectively addressed with Six Sigma. This approach acknowledges the real-world experience of professionals and the limitations of resources within various departments, ensuring a focus on achievable goals that still significantly enhance quality and performance.
Recap about Six Sigma Meaning and Why Six Sigma is called "Six Sigma"
Six Sigma is a comprehensive and data-driven methodology aimed at improving and optimizing business processes to minimize defects and variations. It originated from statistical concepts, particularly focusing on achieving a high level of process capability. The term "Six Sigma" itself refers to the statistical measurement of standard deviations from the mean in a normal distribution. The goal of Six Sigma is to attain a level of performance where only 3.4 defects per million opportunities occur, showcasing a highly efficient and reliable process. This methodology emphasizes the importance of measuring, analyzing, and improving processes to enhance overall quality and customer satisfaction.
The name "Six Sigma" is derived from the statistical concept of sigma, which represents the standard deviation from the mean. In a Six Sigma process, the goal is to achieve a level of performance where the process produces no more than 3.4 defects per million opportunities, indicating an exceptionally high level of quality. The use of "Six" in the term signifies that the goal is to reach a performance level that is six standard deviations away from the mean. This level of precision ensures that processes operate with minimal variability and consistently meet or exceed customer expectations. The name encapsulates the methodology's commitment to delivering exceptional quality by tightly controlling and optimizing processes.
As you delve deeper into the world of Six Sigma, there's a wealth of knowledge and resources available to enhance your understanding. To further your learning journey,
Request today your personal copy of "Six Sigma Framework" book from the International Six Sigma Institute. This free resource offers valuable insights into the principles, methodologies, and practical applications of Six Sigma. By exploring this comprehensive guide, you can gain a deeper understanding of how Six Sigma can drive continuous improvement in various industries, ultimately empowering you to contribute to enhanced efficiency and quality within your own professional endeavors. Download the book today and unlock the potential for transformative change through the principles of Six Sigma.