Six Sigma Process Excellence Disciplines
Process Excellence/Process Documentation:
Process Excellence and Process Documentation helps the project team to define, measure and control the business processes. Six Sigma and Lean tools are used for both Process Excellence and Process Documentation.
Process Excellence and Process Documentation ensures:
- Standardization across different processes in the same organization/department.
- Allows business continuity in case of non-availability of Key Subject Matter Experts (SME’s).
- Helps to understand the current state of the process and also to measure the performance of the future state of the project.
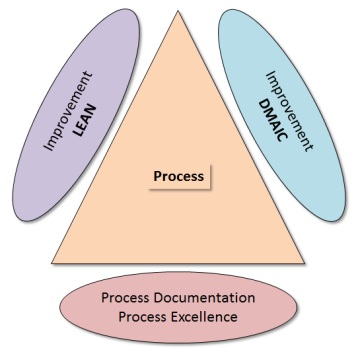
Six Sigma Process Excellence Disciplines
Process Improvement (DMAIC):
Process Improvement is an effort to identify high priority problems in business processes and to train teams to tackle those problems. The methodology used is called DMAIC. It is an acronym for Define-Measure-Analyze-Improve-Control.
In the Define phase, the project is defined. In Measure phase, data is collected, Measurement System is validated and current performance is identified. In Analyze phase, root causes are identified. In Improve, solutions are created and implemented and in Control phase, new performance is sustained).
Lean tools such as Value Stream Map (VSM), Pull and Kaizen are leveraged too.
Process Improvement (Lean):
"Lean" is the set of management practices based on the Toyota Production System (TPS). This methodology is deployed in selected processes to identify and eliminate Non-value added activities and hence increase the operational efficiency. Lean is quick and avoids rigorous data analysis.
There are two critical factors of Lean – Value Added and Non-Value Added. Value is what the customer cares for. It is doing the right things the first time. When we say Value Added, our product or service should add value to the process. Similarly, we should focus on removing non-value added activities from the process.