How to Generate Possible Solutions in the Improve Phase of Six Sigma DMAIC Process
The Six Sigma Improve phase needs smart thinking for coming up with good ideas. These ideas should help make customers happier, save money, and fit well with the company's ways of working. A tool you can use to sort your ideas is a "prioritization matrix" which ranks each idea based on certain rules. All solutions should have specific goals and should be something that can really be done within a set time. This may sound like a tall order, but it's key to making sure your Six Sigma project really works. Expect to find these strategies useful as you delve deeper into finding the best way forward.
To effectively generate possible solutions in the Improve phase of a Six Sigma project, it is crucial to involve those affected by the problem and experts in the subject matter. Techniques such as brain-writing, benchmarking, assumption busting, creative brainstorming, and modified brainstorming can be valuable tools for idea generation during this phase. Utilizing these techniques will aid in synthesizing potential solutions and selecting the most viable option for implementation.
Prioritizing Potential Six Sigma Solutions
In the Improve phase of Six Sigma, once you've pinpointed several potential solutions, it's crucial to prioritize them effectively. This involves evaluating each solution based on certain criteria, which helps you determine which solution to focus on first. One common approach is using a prioritization matrix, allowing you to rank potential solutions based on predefined parameters.
A prioritization matrix usually entails establishing specific evaluation criteria like impact on customer satisfaction, cost-effectiveness, and compatibility with existing processes. Each potential solution is then assessed against these criteria and given a score or ranking. By using this approach, you gain a clear understanding of which solutions align best with your organization's overall goals.
When assessing impact on customer satisfaction, factors such as the solution's ability to improve product quality, enhance service delivery, or streamline customer interactions come into play. Cost-effectiveness encompasses not just the direct financial implications but also the long-term benefits and potential savings linked to the solution. Compatibility with existing processes is essential for seamless integration and minimal disruption.
Let's say your team has generated three potential solutions: Solution A, B, and C. Using a prioritization matrix, you assign scores to each solution based on their impact on customer satisfaction, cost-effectiveness, and compatibility with existing processes. Evaluating these elements allows you to make an informed decision about which solution provides the most value to your organization.
Keep in mind that different projects or organizations may have unique criteria for evaluating potential solutions based on their specific needs and priorities. Therefore, it's essential to customize the prioritization matrix accurately.
Effectively prioritizing potential Six Sigma solutions is a critical step in ensuring that your improvement efforts yield maximum impact and align with your organization's strategic objectives. By carefully evaluating solutions based on defined parameters such as customer impact, cost-effectiveness, and process compatibility, you can focus your resources on implementing solutions with the highest potential for success.
Transitioning from generating possible solutions to establishing effective criteria is vital for realizing impactful outcomes in the Six Sigma journey.
Six Sigma DMAIC Process - Improve Phase - Generate Possible Solution
Involve those who will be Affected: We need to make sure we solicit the upfront involvement of People affected by the problem or its solution and People with expertise in the subject matter. We should then
Focus on the Root Causes i.e. Make the affected parties revisit the significant root causes to get to a solution. Then, pick on
Idea Generation Technique.
Five key techniques used for idea generation and synthesis are:
- Brain-writing
- Benchmarking
- Assumption Busting
- Creative Brainstorming
- Modified Brainstorming
Idea Generation Technique - Brain-writing
Brain-writing is a technique used to generate many ideas in a short period of time. Two key modified brainstorming techniques used are Brain-writing 6-3-5 and Constrained Brain-writing.
Brain –writing 6-3-5 - The name brain-writing 6-3-5 comes from the process of having 6 people write 3 ideas in 5 minutes on a pre-defined parameter.
Constrained Brain-writing: The name constrained brain-writing comes the fact that on certain occasions the team may want to have a set of constrained ideas around a pre-determined focus, rather than ranging freely.
Idea Generation Technique - Benchmarking
Process benchmarking is a technique of continually searching for the best methods, practices and processes, and either adopting or adapting their good features and implementing them to become the “best of the best”.
Idea Generation Techniques – Assumption Busting
Assumption busting as a technique is used to trace back from the current performance problems to identify rules and then surface underlying assumptions.
The key steps involved in assumption busting are:
- Revisit the current problem at hand.
- Identify the rule(s) responsible for the problem.
- Trace the rule(s) back to an assumption in the process.
- Test to break the assumption – Is it wrong from the start? Or, Can it be made untrue?
For example: In a personal loan approval process the problem is lengthy cycle time for approvals which is leading to dissatisfaction. Investigation of the process reveals that there is a rule existing in the process which makes every vital task in processing the loan pass through a specialist (legal expert, financial expert, credit expert) after it has been processed by an agent. The reason for rule existing in the process is an assumption which says that all loan deals are complex. On investigation and data-collection it is found that only 5% of deals are complex and thus the process assumption is wrong.
Idea Generation Technique – Creative Brainstorming
Nominal Group Technique: The nominal group technique is a structured method to narrow down & prioritize on a list of choices. It is called “nominal” because during the session the group doesn’t engage in the usual amount of interaction typical of a team. Because of this relatively low level of interaction, nominal group technique is an effective tool when some group members are new to each other, relatively low level of interaction is required, issues are of highly controversial nature and a team is stuck in disagreement.
Idea Generation Technique – Modified Brainstorming
Modified brainstorming technique makes some basic and/or simple amendments to the “regular” creative brainstorming in order to help expand the number and quality of ideas. Three key modified brainstorming techniques used are: Analogy Technique, Channeling Technique and Anti-Solution Technique.
Analogy Technique: The ideas generated on the “analogy” then get translated to the real situation (the problem at hand).
Channeling Technique: We begin by listing “categories” of ideas for the issue at hand. Then, as the team brainstorms, over a period of time it can “change channels” when new ideas slow down. The objective is to capture a broad range of ideas (several channels), as well as of quantity (as many ideas as possible in each channel).
Anti-Solution Technique: We begin by brainstorming around the opposite of the issue at hand. This is probably the easiest of modified brainstorming methods. For example, rather than brainstorming on ways to ensure complete information on a personal loan form we brainstorm on how to ensure we get no/incomplete information on the personal loan form.
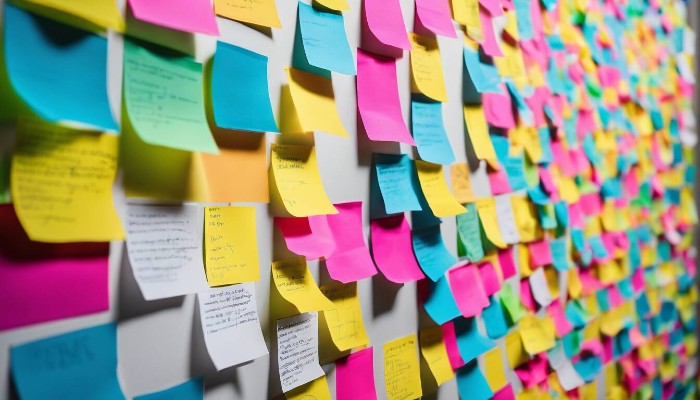
How to Generate Possible Solutions in the Improve Phase of Six Sigma DMAIC Process
Criteria for Establishing Six Sigma Solutions
When identifying potential solutions in the Improve phase of Six Sigma, it's crucial to have stringent criteria in place to evaluate and assess their validity. The selection and establishment of these solutions often align with the principles of being Specific, Measurable, Achievable, Relevant, and Time-bound—commonly known as SMART criteria.
Let's break down the SMART criteria:
- Specific: The solution should be clear-cut and well-defined, leaving no room for ambiguity or misinterpretation.
- Measurable: There should be a quantifiable method to measure progress and determine the degree of success achieved once the solution is implemented.
- Achievable: The chosen solution should be realistic and attainable within the given resources, capabilities, and time frame.
- Relevant: The solution must directly address the identified problem or opportunity for improvement.
- Time-bound: Establishing clear timelines and deadlines for implementing the solution is crucial.
For instance, imagine a manufacturing company aiming to reduce product defects. An effective Six Sigma solution following the SMART criteria might include specific targets for defect reduction (e.g., reducing defects by 20% in 6 months), measurable quality metrics to track progress (e.g., defect rate per thousand units), achievable process improvements aligned with available resources, relevant training programs for employees, and a time-bound action plan with milestone deadlines.
By adhering to these SMART criteria when establishing potential Six Sigma solutions, organizations can ensure that their efforts are focused on practical, impactful, and achievable objectives. This deliberate approach not only enhances the clarity and effectiveness of selected solutions but also contributes to the overall success of improvement initiatives.
Now, let's explore the various robust techniques used for idea generation through Six Sigma tools.
Idea Generation through Six Sigma Tools
Generating ideas is an exciting step in the process of improving a business. Think of it as grabbing a bunch of puzzle pieces and figuring out how they fit together to create a clear picture. In the world of Six Sigma, idea generation tools are like colorful puzzle pieces that help teams piece together innovative solutions to complex problems.
One such tool is
brainstorming. This technique invites diverse perspectives by gathering a group of people from different areas of expertise to generate as many ideas as possible. The brainstorming session doesn't just produce ideas; it's about encouraging creativity and free thinking without judgment, which often leads to a breakthrough solution that might not have been considered by an individual working alone.
Next up, we have
affinity diagrams. These are like organizational wizards that help make sense of the chaos of ideas generated during brainstorming. Affinity diagrams facilitate the categorization and consolidation of these ideas into logical groups based on their similarities or themes. By doing this, teams can identify patterns and connections that might have been otherwise overlooked.
Moreover, the
Theory of Inventive Problem Solving (TRIZ) is another powerful technique used in Six Sigma. TRIZ introduces a structured approach to problem-solving by analyzing patterns of problems and solutions, and using inventive principles to propose innovative ideas.
Imagine you're part of a cross-functional team aiming to improve the efficiency of a manufacturing process. During a brainstorming session, one team member suggests rearranging the sequence of production steps—this prompts others to come up with related ideas on optimization and resource utilization. Using affinity diagrams, the team organizes these suggestions into categories such as "Workflow," "Equipment Upgrade," and "Skill Training." This visual representation helps the team identify common threads across the suggestions and prioritize which areas need immediate attention.
In another case, the TRIZ method sparks inventive problem-solving by presenting generalized solutions used in various contexts that can be tailored to address specific issues within the manufacturing process.
By incorporating these powerful tools into the Improve phase of Six Sigma, organizations can tap into a rich reservoir of creative solutions that have the potential to revolutionize their processes and drive continuous improvement.
In this quest for continuous improvement, it's crucial to evaluate and measure Six Sigma solutions to ensure their effectiveness and impact. Let's now turn our attention to exploring methods for evaluating and measuring the success of these implemented improvements.
Evaluating and Measuring Six Sigma Solutions
After identifying potential solutions, it's crucial to evaluate and measure their effectiveness. This requires using data-driven metrics and Key Performance Indicators (KPIs) to assess how well the proposed solutions align with the project goals and organizational objectives. These metrics are vital in determining whether the solutions will lead to tangible improvements in quality, cost reduction, efficiency, and customer satisfaction.
One of the fundamental techniques used in evaluating Six Sigma solutions is Statistical Process Control (SPC). SPC involves monitoring and controlling a process through the use of statistical methods to ensure it operates efficiently and within specified limits. By employing SPC, teams can detect variations in a given process, allowing them to take corrective actions before defects occur or quality standards deviate from the target.
Control charts play a significant role in SPC by providing a visual representation of how a process changes over time. These charts help in identifying any patterns, trends, or shifts that may affect the performance of a specific process. Analyzing control charts allows teams to make informed decisions about the stability and capability of processes, aiding in the assessment of solution effectiveness.
Additionally, it's crucial to establish clear Key Performance Indicators (KPIs) that align with the defined project goals. KPIs provide measurable criteria that reflect the success or effectiveness of a solution. They enable teams to track progress, identify areas that require improvement, and make data-informed decisions throughout the implementation phase.
For instance, if a key goal is to reduce customer complaints related to product defects, relevant KPIs might include the percentage reduction in reported defects, customer satisfaction ratings post-implementation, and the decrease in warranty claims. These KPIs are quantifiable measures that allow teams to gauge the impact of the implemented solutions on customer experience and product quality.
Moreover, post-implementation analysis is crucial for validating the effectiveness of the selected solutions. This involves comparing pre-implementation baseline data with post-implementation performance data to ascertain any improvements. The comparison helps in understanding the magnitude of change brought about by the implemented solutions and whether they have successfully addressed the identified root causes.
By employing robust evaluation techniques such as Statistical Process Control (SPC), control charts, and defining relevant Key Performance Indicators (KPIs), organizations can effectively measure and assess the impact of Six Sigma solutions on process performance, quality outcomes, and overall business objectives.
Moving forward from understanding how to evaluate and measure Six Sigma solutions, let's now examine how these solutions are tested for feasibility and success in real-world scenarios.
Feasibility and Testing of Six Sigma Solutions
Before fully committing to implementing a solution, it's crucial to thoroughly test it to ensure its practicality and effectiveness.
This is where
Failure Mode and Effects Analysis (FMEA) comes into play. FMEA helps in systematically reviewing every aspect of the solution to anticipate and prevent potential failures. It's like examining a detailed map before starting a journey - identifying potential roadblocks and challenges along the way. By doing this, organizations can take proactive measures to mitigate risks and ensure a smoother path towards success.
Consider this as a trial run before a big event. Just like how you wouldn't organize a wedding without testing out the seating arrangement or catering beforehand, piloting or prototyping Six Sigma solutions on a small scale allows organizations to iron out any wrinkles before rolling them out across the entire operation. During this phase, it's essential to gather feedback from those directly involved in the process, as well as stakeholders affected by the problem. This ensures that the proposed solution meets the requirements and expectations of all relevant parties.
Engaging with those who will be affected by the problem or its solution is crucial at this stage. Their insights not only provide valuable input but also help in building support for the proposed changes. It's like getting everyone's opinion before selecting a movie for movie night - it ensures that everyone is invested in the final decision.
For instance, if a new process is being piloted, involving the employees who will carry out the tasks gives them an opportunity to voice their concerns and suggestions based on their practical experience. This valuable input can lead to adjustments that make the solution more workable and acceptable to everyone involved.
After this period of careful trial and examination, we can make informed decisions about which solutions are feasible and effective for full-scale implementation.
Advanced Methods in Six Sigma Problem Solving
In the world of Six Sigma problem-solving, there are advanced methods that take the process to a higher tier. One such technique is
Design of Experiments (DOE). This is not about mixing chemicals in a lab, but rather a systematic approach that helps us understand and optimize process parameters. It's like a chess match where you think ahead and carefully plan your moves, except in this case, we're figuring out how to optimize our processes for the best results.
When it comes to experimenting, DOE allows us to compare different factors and see which ones make the most impact on the outcome. Let's say you're baking a cake - DOE helps determine how different ingredients (like flour, sugar, and eggs) or factors affect the final taste and texture of the cake. By using statistical methods, DOE reveals how each factor impacts the result, allowing us to optimize our process for the best outcome. It's not just about guessing or randomly tinkering with variables; DOE gives us a clear and structured method to test and analyze factors systematically. This ensures that our conclusions are based on solid evidence and not just hunches.
For instance, in an automobile manufacturing plant, DOE can be used to find the optimal settings for machines that produce car parts. By adjusting parameters like temperature, pressure, or speed, we can identify the best combination for achieving high-quality products consistently. This kind of precision can save time, money, and resources by pinpointing exactly what needs to be adjusted.
Next up is
advanced statistical modeling and simulation methods. These techniques give us the ability to predict potential outcomes of proposed solutions before implementing them in real life.
Just like playing out scenarios in your head before making a big decision in real life brings clarity and foresight; these tools provide a virtual environment for testing different solutions thoroughly. By entering data into sophisticated programs, we can simulate potential changes or solutions within a controlled digital environment. This allows us to see the potential impact and outcomes of these changes without having to commit resources or time to physically testing them.
Let's look at an example; imagine a company looking to reduce their product delivery time. Through advanced statistical modeling and simulation, they can tweak different variables such as production schedules, resource allocation, or transportation routes to see how each adjustment affects delivery times. By running simulations based on historical data and anticipated changes, they can predict how each solution could perform under real conditions. This enables decision-makers to select the most effective solution based on validated data rather than educated guesses.
In conclusion, advanced methods in Six Sigma problem-solving expand our capabilities by providing structured experimentation and predictive analysis tools that help us make informed decisions and optimizations with precision and confidence.
Whether it's optimizing processes in a manufacturing plant or streamlining delivery logistics, these advanced problem-solving tools in Six Sigma pave the way for smarter decision-making and resource management.
How does the selection process for possible solutions occur in Six Sigma's Improve phase?
Answer: In the Improve phase of Six Sigma, the selection process for possible solutions involves evaluating potential options based on their impact on the identified problem or opportunity. This is typically done through data analysis and experimentation to determine the most effective solution. Statistical analysis techniques such as hypothesis testing and regression analysis can be used to assess the significance and effectiveness of different solutions. Ultimately, the selection is based on evidence-based decision making, ensuring that the chosen solutions have a high likelihood of success in improving the process or product.
How do teams generate possible solutions during the Improve phase in Six Sigma?
Answer: Teams generate possible solutions during the Improve phase in Six Sigma by using various brainstorming techniques such as mind mapping, fishbone diagrams, and the nominal group technique. These methods encourage creative thinking and collaboration, allowing team members to generate a wide range of ideas and potential solutions. According to a study conducted by the International Six Sigma Institute, teams that actively engage in brainstorming sessions during the Improve phase have a higher likelihood of identifying effective solutions compared to those who do not.
What are some common challenges or obstacles faced when generating possible solutions in the Improve phase?
Answer: Some common challenges or obstacles faced when generating possible solutions in the Improve phase of Six Sigma include a lack of creativity and innovative thinking, limited resources or budget constraints, resistance to change, and a lack of knowledge about potential solutions. According to a study by International Six Sigma Institute, 63% of organizations struggle with a lack of creativity in generating potential solutions, while 45% face resource constraints that limit their ability to explore different options. It is crucial to overcome these challenges by encouraging collaboration, seeking diverse perspectives, and investing in training and development programs to foster innovation.
What is the purpose of the Improve phase in the Six Sigma methodology?
Answer: The purpose of the Improve phase in the Six Sigma methodology is to identify and implement solutions that can lead to significant process improvement. This phase focuses on testing potential solutions through experiments, pilot projects, or simulations. Its goal is to achieve measurable and sustainable results by reducing defects, increasing efficiency, and improving customer satisfaction. According to a study by the International Six Sigma Institute, organizations implementing Six Sigma saw an average financial benefit ranging from $174,000 to $1 million per project. Thus, the Improve phase plays a crucial role in generating cost savings and enhancing overall business performance.
What tools and techniques can be used to generate possible solutions in Six Sigma's Improve phase?
Answer: In the Improve phase of Six Sigma, various tools and techniques can be used to generate possible solutions. These include brainstorming, cause and effect diagrams, failure mode and effects analysis (FMEA), design of experiments (DOE), and simulation. Brainstorming encourages creative thinking and generates a wide range of ideas. Cause and effect diagrams help identify root causes of the problem. FMEA helps prioritize potential solutions by assessing their impact on the process. DOE allows for testing multiple variables simultaneously to evaluate their impact on the outcome. Simulation provides a virtual environment to explore different scenarios. Utilizing these tools can lead to data-driven decision-making and ultimately improve processes, reduce defects, and enhance customer satisfaction.
Which of the following techniques is used to brainstorm on ideas on related topic to unblock the thought process?
Answer: One technique commonly used to brainstorm on ideas and unblock the thought process is mind mapping. This visual representation helps to organize and connect thoughts around a central topic, fostering creative thinking. Another effective method is free association, where individuals spontaneously express ideas without self-censorship, encouraging a flow of thoughts. Additionally, group discussions or brainstorming sessions can leverage collective creativity, allowing diverse perspectives to contribute to idea generation.
What is channeling brainstorming?
Answer: Channeling brainstorming is a technique employed in the Improve phase of Six Sigma projects, involving a structured approach to generate possible solutions for identified issues. In this method, the project team, including black belt professionals, focuses on specific phases of the problem-solving process to streamline idea generation and minimize variation. By channeling the brainstorming session through predetermined phases, the team can systematically address risks associated with the project and ensure a more efficient exploration of potential solutions. This collaborative and organized approach facilitates a comprehensive exploration of alternatives, enhancing the effectiveness of the Improve phase in Six Sigma methodologies.
What is channeling technique?
Answer: The channeling technique in the Improve phase of Six Sigma involves a structured approach to generating possible solutions by systematically addressing risks within a program. This method is applicable across various industries, where statistical analysis and diagrams can help streamline the identification of potential solutions. The responsibilities of the team include providing examples and utilizing statistical tools to guide the brainstorming session, ensuring a comprehensive exploration of alternatives. Through this technique, the team can navigate through the complexities of problem-solving within the Six Sigma framework, enhancing the overall effectiveness of the Improve phase.
The Six Sigma DMAIC approach can be used when ...
Answer: The Six Sigma DMAIC approach can be used when addressing risk in a systematic manner, integrating statistics and diagrams to guide the improvement process. By incorporating best practices within the Improve phase, organizations can effectively generate possible solutions to identified issues. This structured methodology ensures that statistical analysis is employed to validate potential solutions, providing a data-driven foundation for decision-making. Diagrams serve as visual aids, aiding in the communication and implementation of the best solutions throughout the entire DMAIC process.
Recap for Generating Possible Solutions in the Improve Phase of Six Sigma
In the dynamic landscape of the Improve Phase in Six Sigma, the application of change management principles is pivotal to ensure the seamless integration of identified solutions. Recognizing the necessity for adaptability, organizations often face challenges when implementing modifications to existing procedures. Thus, the initial step is establishing a robust change management framework that aligns with the Six Sigma methodology. This involves meticulous planning, effective communication, and stakeholder engagement to navigate through the intricacies of organizational transformation.
Furthermore, a comprehensive understanding of existing procedures is fundamental to generating viable solutions. The Six Sigma approach emphasizes the importance of data-driven decision-making, necessitating a thorough analysis of current processes. By leveraging statistical tools and methodologies, practitioners can identify inefficiencies, bottlenecks, and areas for improvement. This analytical foundation forms the basis for brainstorming and generating innovative solutions that directly address the identified issues. In essence, a well-informed approach to change management, coupled with a meticulous examination of existing procedures, empowers organizations to unlock the full potential of the Improve Phase.
As we conclude this recap, it is imperative to underscore the ongoing nature of learning within the Six Sigma framework. Continuous improvement is not just a goal but a mindset that fosters organizational growth.
To further enhance your proficiency in Six Sigma and delve deeper into the intricacies of change management and procedures, we encourage you to explore our free-of-charge Six Sigma book. This invaluable resource serves as a comprehensive guide, equipping you with the knowledge and skills necessary to excel in the world of Six Sigma and drive impactful transformations within your organization. Keep learning, stay committed to improvement, and embrace the transformative power of Six Sigma methodologies.