FMEA in Six Sigma DMAIC
Failure Mode and Effect Analysis
FMEA, short for Failure Modes and Effects Analysis, is a powerful tool utilized in the Six Sigma DMAIC approach to spot and block potential product or process problems before they surface. Integrated within the "Analyse" stage of Six Sigma's Define-Measure-Analyse-Improve-Control (DMAIC) framework, it predicts where failures might occur, gauges their impact on customer experience, and shapes prioritization of fix-it actions with an eye on highest risk areas. Contrary to what you may think, this isn't just about nipping issues in the bud - it's also a creative funnel to elevate product quality and minimize hiccups, whether in existing processes or when forging new ones. Just wait till we delve into the techniques.
Integrating FMEA into the Six Sigma DMAIC process involves identifying potential failures, assessing their impact, and prioritizing improvement efforts based on risk priority numbers. By using FMEA in this way, project teams can enhance product quality and reduce errors by modifying existing processes or creating new ones to correct potential defects.
What is FMEA and Its Role in Six Sigma DMAIC
Failure Modes and Effects Analysis, or FMEA, may seem complex, but it's a methodical approach for identifying and preventing problems before they occur. In the context of Six Sigma DMAIC, FMEA plays a critical role in the "Analyze" phase where project teams predict potential failures, estimate their impact on the customer experience, and prioritize improvement efforts based on the highest risk priority numbers.
Think of FMEA as similar to a crystal ball—just like a fortune teller gazes into a crystal ball to see what lies ahead, project teams use FMEA to anticipate possible problems in their processes. Instead of predicting the future, they're identifying potential defects in production processes. This proactive approach allows them to modify existing processes or create new ones to correct these potential defects before they can cause any real harm.
By employing FMEA, teams enhance product quality and reduce errors within existing processes, leading to better products and more satisfied customers.
One thing that sets FMEA apart from other tools is its focus on the impact a failure can have on the customer experience. Addressing occurrence—the likelihood of a defect occurring during production—can significantly influence how customers perceive products or services.
For instance, imagine a company manufacturing headphones; a wiring issue during production might lead to faulty headphones reaching customers. Using FMEA to identify potential failures early on helps address issues before they affect customers, ensuring satisfaction and trust remain intact.
So, FMEA serves as more than just another tool—it's akin to a reliable crystal ball that reveals potential process pitfalls, facilitating resolution before customer impact occurs.
Intrigued by the power of FMEA? Now let's delve into the specific techniques for deploying FMEA effectively within the Six Sigma DMAIC methodology.
Failure Mode and Effect Analysis (FMEA) in Six Sigma
FMEA identifies all the probable failure modes for the product or process. It prioritizes the failure modes for focused attention by using a scoring model based on:
- S: Severity
- O: Occurrence
- D: Detectability
- RPN: Risk Priority Number
RPN = S x O x D
Based on the above suitable action plans can be created to contain the risk. It is used as a living document and could be a good foundation for building robustness.
Definition of Terms:
- Failure Mode – The way in which a specific process input fails
- Effect – The impact the failure has on the Critical Quality Parameter
- Cause – The source of variation that caused the process to fail
- Current controls – Systemized devices in place to prevent or detect the failure
- Severity – Importance of an effect on critical quality parameter (1-Not severe; 10 – very severe)
- Occurrence – Frequency with which a cause occurs (1-Not likely; 10-Very likely)
- Detection – Ability of current control to detect the cause before creating a failure mode (1-likely to detect; 10-not likely to detect)
- RPN is an acronym for Risk Priority Number. It is calculated by multiplying the Severity, Occurrence and Detectability.
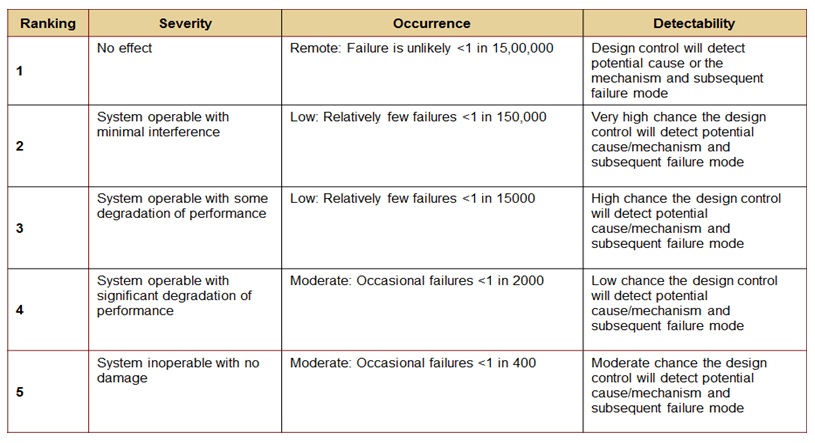
Failure Mode Effect Analysis (FMEA) - 1
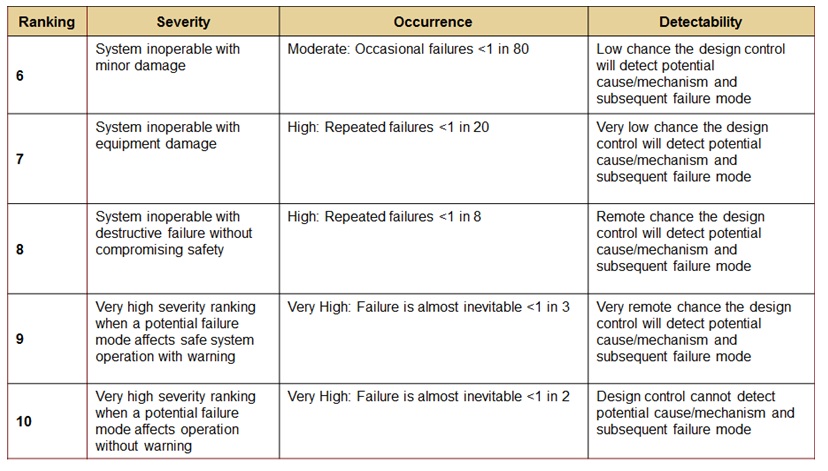
Failure Mode Effect Analysis (FMEA) - 2
Techniques for Using FMEA in Six Sigma DMAIC
When it comes to using FMEA effectively, the first step is to identify potential failures in your process or product. This involves compiling a comprehensive list of all possible failure modes and their effects on the overall process. To ensure that no potential failure goes unnoticed, techniques like brainstorming and historical data analysis are invaluable tools. Brainstorming sessions can engage diverse perspectives, giving you an expansive view of potential risks, while historical data analysis provides a record of past issues and risks, feeding into a more thorough assessment.
Let's take a moment to delve deeper into this concept. Brainstorming with a cross-functional team can bring different viewpoints and experiences to the table, helping to uncover potential sources of failure that may not have been immediately obvious. By leveraging diverse expertise, you create a comprehensive list of potential failures that covers all aspects of the process or product. Furthermore, historical data analysis offers insights into previous problems, enabling a proactive approach in addressing known failure modes before they become critical issues.
Next comes the critical step of measuring the impact and severity of each identified potential failure mode. This assessment involves rating each failure mode on a ten-point scale to prioritize issues based on their severity and potential impact on the end customer or user.
The impact and severity rating is a crucial phase in the FMEA process. By quantifying the impact and severity of each identified potential failure mode, the project team gains clarity regarding which issues require immediate attention and which ones can be addressed at a later stage. This enables efficient resource allocation and prioritization of improvement efforts based on the most critical failure modes.
Additionally, assessing the likelihood of each potential failure occurring is equally vital. This evaluation involves analyzing the current process controls and detection methods to determine the probability of detecting the error before it impacts the end customer.
The likelihood of failure and detection assessment is an opportunity to scrutinize existing process controls and detection mechanisms critically. Through this analysis, project teams can identify gaps or weaknesses in current detection methods, enabling them to strengthen controls where needed and prioritize efforts towards enhancing detection capabilities for high-risk failure modes. This proactive approach aligns with Six Sigma's focus on enhancing product quality by modifying processes to prevent or swiftly rectify potential defects.
At this point, we have outlined how brainstorming and historical data analysis aid in identifying potential failures, as well as the significance of assessing impact, severity, likelihood of failure, and detection in optimizing FMEA effectiveness. In our next section, we will further explore strategies for prioritizing improvement efforts based on these assessments.
Benefits and Impact of FMEA in Six Sigma DMAIC
FMEA acts like a guardian angel for production processes—it doesn't just identify potential defects; it provides a roadmap for tackling them systematically, efficiently, and with a sharp focus on the customer experience. Let's uncover the invaluable benefits and impacts of employing FMEA within the Six Sigma DMAIC framework.
Objective Measurements of Defects
FMEA is more than just a list of hypothetical "what-ifs"; it offers a precise, methodical way to measure potential defects and quantify their probable impacts. By doing so, it provides project teams with an empirical foundation for problem-solving, enabling them to address issues based on hard evidence rather than vague suspicions or assumptions.
This approach allows teams to evaluate and prioritize specific areas of concern with clarity and confidence, ensuring that resources are directed toward the most critical aspects of the production process.
Prioritizing Improvement Efforts
One of the significant advantages of FMEA lies in its ability to pinpoint high-risk elements within production processes. By calculating risk priority numbers (RPN) based on factors such as occurrence, severity, and detection, project teams gain insights into which issues pose the greatest threats to quality, efficiency, and customer satisfaction.
By zeroing in on these higher-risk areas, organizations can concentrate their improvement efforts where they matter most, enhancing the effectiveness of their overall process enhancement initiatives. This targeted strategy helps streamline resources and avoids wasting time and effort on less critical aspects that would have minimal impact if improved.
Focus on Customer Impact
Addressing occurrence—the likelihood of a failure happening—has a profound impact on customer experience, aligning strongly with Six Sigma's core principle of driving process improvements based on customer feedback.
By acknowledging and addressing potential failures that could directly affect customers, organizations demonstrate their commitment to delivering high-quality products or services that meet or exceed customer expectations. This approach elevates customer satisfaction, fosters brand loyalty, and strengthens market competitiveness—a trifecta of benefits that solidify the pivotal role of FMEA within the Six Sigma DMAIC methodology.
In summation, the symbiotic relationship between FMEA and Six Sigma DMAIC not only empowers organizations to detect and mitigate defects but also infuses their improvement efforts with purposeful precision while ensuring a laser-like focus on delivering exceptional experiences to their customers.
Moving forward, we will now explore the nuts and bolts of the Six Sigma DMAIC methodology and how it effectively streamlines process improvements.
Understanding the Six Sigma DMAIC Methodology
The Six Sigma DMAIC Methodology is an invaluable tool for process improvement, comprising five crucial phases: Define, Measure, Analyze, Improve, and Control. Each phase plays a vital role in streamlining processes, reducing defects, and enhancing overall quality.
Define: Setting Clear Goals
In the Define phase, project teams establish clear project goals and deliverables. This is where the emphasis lies on understanding the customer's requirements and identifying potential areas for improvement. It's essential to define the project scope, objectives, and specific metrics that will be used to measure success. By clearly defining the problem and its impact on the customer or business, project teams can secure stakeholder alignment and set the foundation for subsequent phases.
Remember: The key to successful process improvement is aligning project goals with customer needs.
Measure: Establishing a Baseline
Once the objectives are well-defined, project teams move into the Measure phase. Here, they focus on establishing the current performance of the process by collecting relevant data and identifying the root cause of any identified issues. This phase enables the team to gather valuable information that will serve as a baseline for comparison throughout the improvement process. With a comprehensive understanding of the process's current state, project teams can effectively pinpoint areas for enhancement.
For instance, if a manufacturing company is experiencing a high defect rate in a specific product line, the Measure phase entails meticulously collecting data around production processes, defect occurrences, and customer feedback to uncover the precise sources of inefficiency or defects.
Analyse: Identifying Improvement Opportunities
During the Analyze phase, project teams leverage various analytical tools such as FMEA to identify and evaluate potential process failures rigorously. By conducting thorough assessments using FMEA (Failure Mode and Effects Analysis), project teams can prioritize improvement opportunities and gain enhanced insights into the causes of defects. This depth of analysis allows for precise identification of critical areas that need attention.
THE IMPROVEMENT JOURNEY
From here on out—in the next stage—Improvement becomes the core focus.
Now that we've laid down the foundational pillars of Six Sigma DMAIC methodology, it’s time to witness its practical application through a compelling real-world case study.
Case Study: Real-World Application of FMEA in Six Sigma DMAIC
Picture a company that manufactures automotive parts. They were grappling with increased customer complaints about the quality and reliability of a critical product—the transmission control module. It was leading to significant operational downtime for their clients, resulting in dissatisfaction and tarnishing the company's reputation in the market.
The company resolved to apply the Six Sigma DMAIC methodology, focusing specifically on Failure Mode and Effects Analysis (FMEA) to systematically address these challenges.
Firstly, they scoped out the project by defining the problem clearly, along with specific customer requirements related to product quality and performance. In this step, they identified that the failure modes could be related to electrical failures, software glitches, or mechanical issues within the transmission control module. After identifying the potential failure modes, they assessed the impact each one could have on the overall functionality and safety of the product. This allowed them to prioritize which failure modes needed immediate attention and which could be addressed at a later stage.
With an understanding of the failure modes and their potential effects on the product and customer satisfaction, they then quantified and ranked each failure mode based on severity, occurrence, and detection. This became invaluable in determining where resources should be allocated to make the most impactful improvements.
For instance, they discovered that a particular software glitch had a high severity rating due to its potential impact on critical functions of the transmission control module and occurred frequently enough to warrant immediate attention. Armed with this insight, they were able to direct their corrective actions towards addressing this specific issue which led to a substantial improvement in product reliability.
This application of FMEA within the DMAIC framework enabled the company to not only identify and understand potential failure modes but also take decisive action to address them effectively. The result was a noticeable improvement in process quality and customer satisfaction.
This real-world example highlights how FMEA, when strategically applied within the Six Sigma DMAIC framework, can lead to tangible improvements in product quality, customer satisfaction, and ultimately contribute to business success.
Now, armed with insights from real-world applications of FMEA, let's explore effective strategies for further enhancing its impact within the Six Sigma DMAIC framework.
Strategies for Enhancing FMEA Effectiveness in Six Sigma DMAIC
In the world of process improvement, cross-functional collaboration is akin to a secret ingredient that enhances the entire process. By harnessing input from various departments like production, engineering, quality assurance, and customer service in the FMEA process, you ensure a more comprehensive evaluation, leading to a more accurate identification of potential failure modes.
Imagine this: You're baking a cake. Each person involved—someone who gathers ingredients, a mixer, an oven operator—plays a unique and crucial role in ensuring that the final product comes out just right. Similarly, when it comes to FMEA in Six Sigma DMAIC, engaging various departments ensures that all aspects of a process are thoroughly evaluated. This collaborative approach leads to a more holistic analysis and improves the accuracy of identifying potential failure modes.
For instance, imagine developing a new software system without involving the IT team in the FMEA process. It might result in major blind spots where certain potential failures aren't fully anticipated or addressed. When everyone's expertise comes into play, issues can be spotted earlier and corrected more effectively.
Next, let's talk about training and education. As with any tool or method,
adequate training and education are critical to ensure that team members involved in FMEA processes can effectively apply its methods and understand its role in the DMAIC methodology.
When you learn a new recipe or pick up a new hobby, you start with learning the basics before moving on to more advanced techniques. Similarly, understanding how FMEA integrates into the larger DMAIC process is vital for employees involved in process improvement projects. Without proper training and education on how to apply FMEA effectively, errors may be overlooked, impacting overall product quality.
Suppose someone tries to bake a cake without knowing what precise measurements are needed for each ingredient. The result could be disastrous. In the same way, if team members lack adequate training and understanding of FMEA principles and methodology, they might miss potential failure modes or assign inaccurate severity ratings during analysis.
Now let's discuss how integrating customer feedback into the FMEA process aligns improvement efforts with customer expectations and satisfaction.
Integration with Customer Feedback
Customer feedback is like having a secret map to fulfilling your customers' needs and expectations. By integrating insights from customer feedback into your FMEA process, you align improvement efforts with what matters most - customer satisfaction.
In essence, imagine driving along a road without a map or GPS - you might reach your destination eventually, but there will likely be wrong turns and detours along the way. Similarly, by not integrating customer feedback into your FMEA process...
it's like setting off on your journey of improvement without knowing your customers' needs and preferences - a recipe for wandering off course!
For example, let's say you're planning improvements to an online shopping platform without considering customer feedback on usability issues. The result could be changes that fail to address crucial pain points for users.
By integrating customer feedback into the FMEA process, teams can prioritize improvement efforts based on real customer experiences rather than assumptions or conjecture.
Ensuring effective FMEA implementation involves diverse perspectives from various departments, comprehensive training and education for staff involved, as well as integrating valuable customer feedback into improvement initiatives. This ensures a more accurate identification of potential failures and aligns improvement efforts with customer expectations.
FAQ for FMEA (Failure Mode and Effect Analysis) in Six Sigma
How does FMEA contribute to the Six Sigma DMAIC methodology?
Answer: FMEA (Failure Mode and Effects Analysis) plays a crucial role in the Six Sigma DMAIC (Define, Measure, Analyze, Improve, Control) methodology by identifying potential failure modes and their effects on processes. Through FMEA, teams can prioritize improvement initiatives and develop proactive strategies to mitigate risks and reduce defects. Studies have shown that integrating FMEA into the DMAIC approach leads to significant improvements in process performance, customer satisfaction, and waste reduction (source: Measuring Process Capability in Six Sigma DMAIC Projects: An Empirical Study).
What are the key steps involved in implementing FMEA within the Six Sigma DMAIC framework?
Answer: The key steps involved in implementing FMEA within the Six Sigma DMAIC framework include: (1) Define the scope and objectives of the process, (2) Identify potential failure modes and their impact on the process, (3) Determine the likelihood and severity of each failure mode, (4) Prioritize failure modes based on risk priority numbers (RPN), (5) Develop and implement actions to mitigate or eliminate high-risk failure modes, and (6) Monitor and control the process to ensure sustainability. According to a study by Han et al., implementing FMEA within DMAIC significantly improved process performance, reducing defects by an average of 35% and cycle time by 25%.
Are there any best practices or tips for effectively using FMEA in Six Sigma DMAIC projects?
Answer: Yes, there are several best practices and tips for effectively using FMEA in Six Sigma DMAIC projects. Firstly, ensure good team collaboration by involving all stakeholders in the FMEA process to gather different perspectives and expertise. Secondly, prioritize risks based on severity, occurrence, and detection ratings to focus improvement efforts on critical areas. Additionally, use historical data and lessons learned to inform risk assessments. Finally, regularly update and review the FMEA throughout the project life cycle to reflect new information or changes. Studies have shown that following these best practices leads to more accurate risk assessments and better outcomes in process improvement projects (source: "A Comparative Study of Six Sigma Tools for Process Improvement", Journal of Quality Engineering).
What does FMEA stand for in Six Sigma DMAIC?
Answer: FMEA stands for Failure Mode and Effects Analysis in Six Sigma DMAIC. It is a systematic and proactive method used to identify potential failures or risks in a process and evaluate their impact on the final outcome. FMEA helps in prioritizing improvement efforts by quantifying the severity, occurrence, and detection of each failure mode, helping teams focus on high-priority issues with the most significant impact on quality and efficiency. According to a study published in the International Journal of Engineering Research and General Science, FMEA has proven to be an effective tool in reducing defects and improving process performance by up to 40%.
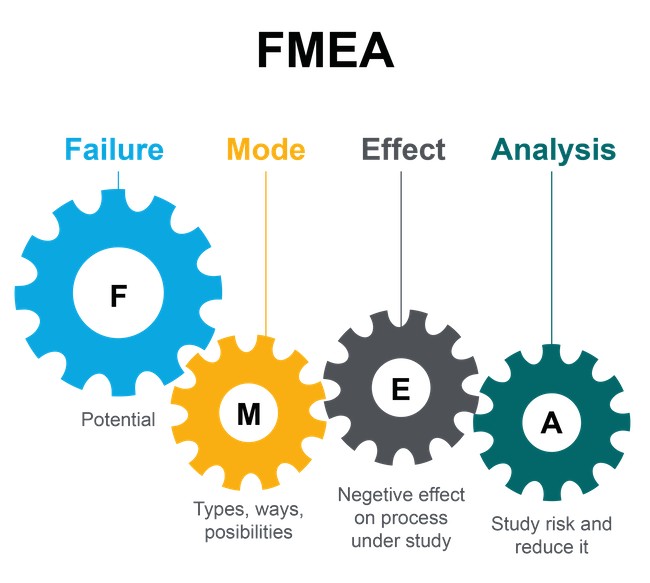
FMEA Six Sigma - Failure Mode & Effect Analysis
What are some real-world examples of successful applications of FMEA within the context of Six Sigma DMAIC?
Answer: Some real-world examples of successful applications of FMEA within the context of Six Sigma DMAIC include reducing defects in automotive manufacturing, improving patient safety in healthcare, and enhancing product reliability in the electronics industry. For instance, a case study conducted by General Motors successfully implemented FMEA to reduce defects in their gearbox assembly process, resulting in an estimated annual savings of $1.2 million. Another study carried out in a hospital setting revealed a significant decrease in medication errors by implementing FMEA, leading to improved patient safety. Furthermore, companies such as Apple have utilized FMEA to enhance the reliability of their products by identifying potential failure modes early on. These examples demonstrate how FMEA, when employed within Six Sigma DMAIC, can yield tangible improvements and cost savings.
What is FMEA Six Sigma?
Answer: FMEA, or Failure Mode and Effect Analysis, is a crucial part of the Six Sigma methodology, specifically within the DMAIC (Define, Measure, Analyze, Improve, Control) framework. It serves as a systematic approach to identify and assess potential failure modes in various processes across industries. By assigning a score to each failure mode based on factors like severity, occurrence, and detection, FMEA helps prioritize risks and focus efforts on areas that require improvement. This analytical tool is applied at different levels, including design and process, offering organizations valuable insights into ways to enhance reliability and efficiency. FMEA is integral to preventive measures and continuous monitoring, contributing to knowledge-driven process control in diverse industrial settings.
What is the purpose of FMEA in Six Sigma?
Answer: The purpose of Failure Mode and Effect Analysis (FMEA) in Six Sigma is to systematically identify, assess, and prioritize potential failure modes in a process. FMEA serves as a preventive tool by proactively addressing potential issues and their effects on the desired outcomes. Through rigorous documentation, FMEA helps the organization validate and verify the critical aspects of a process, ensuring that it aligns with Six Sigma principles. By examining failure modes at each level of a process, FMEA assists in asking pertinent questions that enhance the organization's understanding of potential risks, providing a structured approach to minimize the chance of failures and improve overall process performance. This structured analysis contributes to the overall success of the Define-Measure-Analyze-Improve-Control (DMAIC) methodology within the Six Sigma framework.
What tools are commonly used in FMEA analysis?
Answer: In Failure Mode and Effect Analysis (FMEA) within the Six Sigma DMAIC framework, several tools are commonly employed to enhance the analysis process. Prevention is a key focus, and tools such as Process FMEA (PFMEA) help identify potential failure modes early in the process, allowing for proactive measures. Verification and validation tools, including Design FMEA (DFMEA) and System FMEA (SFMEA), ensure that design and system-level considerations are thoroughly assessed for potential risks. Different types of FMEA, such as Functional FMEA and Design FMEA, address various stages of the process. Access to historical data and lessons learned is vital for comprehensive FMEA, enabling a more informed analysis and aiding in continuous improvement efforts.
What are some examples of successful implementation of FMEA in Six Sigma projects?
Answer:
- One notable success story of FMEA implementation in a Six Sigma DMAIC project involved a manufacturing company that significantly reduced defects in their production line by systematically identifying and mitigating failure modes in key processes.
- In a healthcare setting, a Six Sigma project utilized FMEA to enhance patient safety by proactively addressing potential failure modes in medication administration processes, resulting in a substantial decrease in medication errors.
- A software development firm achieved improved product quality and customer satisfaction by incorporating FMEA into their Six Sigma methodology, identifying and addressing software bugs and potential failure modes early in the development lifecycle.
- An automotive industry example showcases the effectiveness of FMEA in a Six Sigma initiative, where a company successfully minimized product recalls and enhanced reliability by applying FMEA principles to analyze failure modes in critical components of their vehicles.
- In the aerospace sector, a Six Sigma project utilized FMEA to enhance the design and manufacturing processes, resulting in a reduction of defects in critical components, increased reliability, and compliance with stringent safety standards.
These examples highlight the versatility and success of FMEA application in various industries within the Six Sigma DMAIC framework.
What are the key components of FMEA?
Answer: Failure Mode and Effect Analysis (FMEA) is a systematic approach utilized within the Six Sigma DMAIC (Define, Measure, Analyze, Improve, Control) framework to identify and mitigate potential failures in processes. The key components of FMEA include a thorough examination of failure modes, their effects, and the criticality of those effects. This analysis involves interdisciplinary collaboration among black belt professionals who possess expertise in various aspects such as materials, compliance, and methodologies. FMEA aims to prioritize potential risks by assigning a risk priority number (RPN) to each failure mode, facilitating targeted improvement efforts within the Six Sigma methodology
.
What industries use FMEA analysis in Six Sigma?
Answer: FMEA analysis in Six Sigma is widely employed across various industries, including manufacturing, healthcare, automotive, aerospace, and technology. Organizations implementing Lean Six Sigma methodologies often integrate Failure Mode and Effect Analysis (FMEA) as a crucial tool within the Define-Measure-Analyze-Improve-Control (DMAIC) framework. Professionals seeking expertise in FMEA can undergo Lean Six Sigma certification programs and courses to enhance their skills and contribute effectively to process improvement initiatives within their respective industries.
Recap for FMEA (Failure Mode and Effect Analysis) in Six Sigma
In retrospect, Failure Mode and Effect Analysis (FMEA) stands as a pivotal component within the Six Sigma methodology, particularly in the DMAIC (Define, Measure, Analyze, Improve, Control) framework. It serves as a proactive tool to identify potential failure modes in processes, allowing organizations to preemptively address issues and enhance overall performance.
Through a meticulous analysis of failure modes and their potential effects, FMEA contributes significantly to risk mitigation and continuous improvement.
As we delve into the realm of FMEA in Six Sigma, it becomes evident that embracing a culture of continuous learning is paramount. The journey of process improvement is dynamic, and staying abreast of emerging methodologies and best practices is essential for sustained success.
To empower yourself further in the realm of Six Sigma, we invite you to explore our free of charge Six Sigma training book. By taking this proactive step, you not only enhance your understanding of FMEA but also position yourself as an adept practitioner ready to navigate the complexities of process improvement with confidence. Seize the opportunity to elevate your skills and propel your organization towards excellence - request your complimentary Six Sigma training book today!