Six Sigma DMAIC Problem Statement & Project Charter
Guide and Examples to Develop a Problem Statement and the Six Sigma DMAIC Project Charter
Project Charter is a document that provides a framework and objective for a Six Sigma Process Improvement and/or Problem-solving Project. The problem statement plays a vital role in the Six Sigma DMAIC Project Charter, serving as a key element that initiates the investigation, leading to the discovery of more information and the identification of the root cause.
Crafting a problem statement for a Six Sigma DMAIC project charter is like drawing a map. It offers direction and focus, ensuring your project doesn't veer off course. Insights specific to the problem at hand, such as peculiarities in data trends or unique customer complaints, become the landmarks here. These key details follow a path that leads you to your target -- an efficient, quality-controlled process.
To craft a precise problem statement for your Six Sigma DMAIC project charter, define the issue to be addressed, specify the exact location and process involved, provide supporting facts such as frequency and quantity, highlight the financial impact, and focus solely on the area of concern without assigning blame or suggesting solutions at this stage. Remember that the problem statement is a crucial component of the Six Sigma DMAIC Project Charter and sets the stage for the investigation to uncover additional information and identify the root cause.
Six Sigma DMAIC Project Charter
The DMAIC project charter is akin to the blueprint for your project. It provides a clear outline of the project's purpose, the scope of work, expected benefits, and the required resources.
By defining these fundamental aspects at the onset of a project, the charter sets the foundation for success. It acts as a guiding beacon for everyone involved, ensuring that all stakeholders are on the same page and have a comprehensive understanding of the mission and objectives to be achieved.
The
purpose statement within the charter elucidates the primary goal of the project and why it is being undertaken. This creates a shared vision among team members, aligning their efforts towards a common objective. Furthermore, it serves as a reference point throughout the project, assisting in decision-making and prioritization.
Imagine running a marathon without knowing where the finish line is. The purpose statement in the project charter acts as that essential finish line—a tangible goal that provides direction and motivation to keep moving forward.
Moving on to the
scope, this section outlines the boundaries of the project - what is included and perhaps more importantly, what is not included. Clearly defining the scope prevents unnecessary deviations and ensures that the project stays focused on its intended objectives.
Failing to establish a clear scope is akin to embarking on a road trip without a map. You might end up taking unnecessary detours and get lost along the way.
Additionally, expected
benefits are elucidated in the charter, offering a preview of what accomplishments can be anticipated upon successful completion of the project. This not only motivates stakeholders but also serves as a yardstick by which to measure success.
With this comprehensive roadmap in place, all team members are equipped with a clear understanding of their roles and responsibilities, ensuring that everyone is aligned towards achieving success in every stage of the DMAIC process.
Now equipped with a robust understanding of setting up a project charter, let's shift our focus to crafting an effective problem statement.
Preparing a Problem Statement
When defining the problem at hand, clarity is key. The problem statement should be concise and specific, focusing on the issue without placing blame. It's about identifying an area for improvement, whether it's reducing defects, enhancing efficiency, or addressing any other process inadequacies.
It should be based on factual evidence and pinpoint exactly what needs to improve. For instance, if there has been a significant increase in defect rates or a reduction in customer satisfaction due to operational inefficiencies, these specifics need to be clearly articulated in the problem statement.
Here’s a scenario: If you notice that product defects have increased by 15% over the last quarter and this has led to a 20% reduction in customer satisfaction, these specific figures should be included in the problem statement. Quantitative data brings credibility and urgency to the issue at hand, making it easier for stakeholders to comprehend the gravity of the situation.
The problem statement isn't just about pointing out flaws – it's about highlighting areas for potential improvement. By incorporating quantitative data pertaining to things like frequency, quantity, duration, and financial impact, you provide a clearer picture of the magnitude of the issue. This aids in aligning stakeholders' perspectives on the severity of the problem and ultimately facilitates buy-in for future improvement initiatives.
Incorporate quantitative data that illustrates the issue. This might include information on frequency, quantity, duration, and the financial impact on the organization.
At this stage, it's crucial to steer clear of proposing any solutions. The problem statement should strictly delineate the problem and its impact—leaving room for solutions to be formulated during the analysis phase. This ensures that all focus remains on defining the core issue before jumping into devising remedies.
As we can see, preparing a problem statement demands careful consideration and precision. It's not just about identifying problems but rather about setting up a solid foundation for efficient resolution strategies and driving impactful improvements within processes.
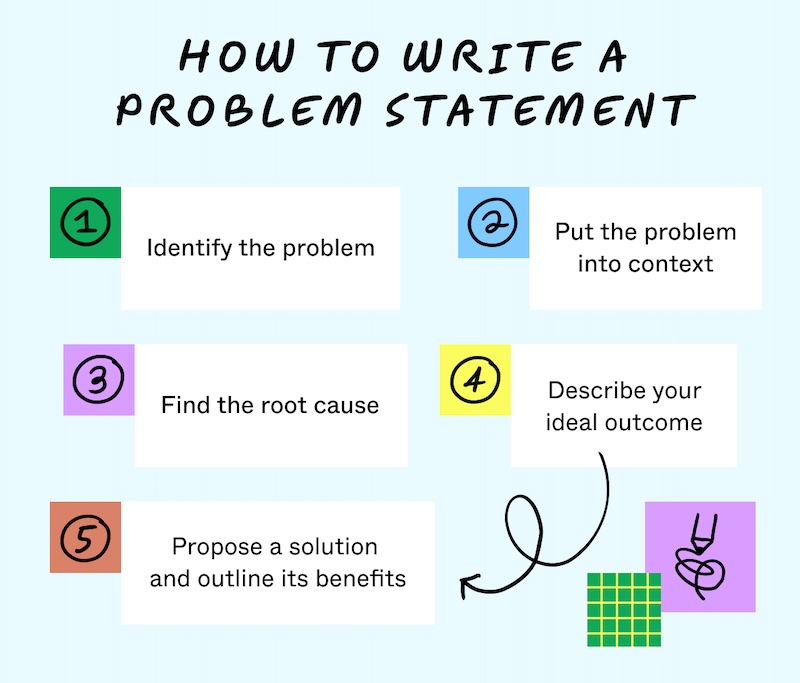
Six Sigma DMAIC Project Charter Problem Statement
Setting Project Objectives
When establishing your project objectives, it's crucial to ensure they adhere to the SMART criteria—Specific, Measurable, Achievable, Relevant, and Time-bound. By setting SMART goals, you guarantee that your objectives are clear, attainable, and aligned with the overall vision of your Six Sigma project.
Let's break down what each letter in "SMART" stands for:
- Specific: Your objective should address a specific area for improvement in your process. It shouldn't be vague or open to interpretation. This will help you stay focused on what you're trying to achieve.
- Measurable: There should be a clear way to measure progress toward the objective. For example, if your goal is to reduce defects, you should be able to track and quantify the decrease in defects over time.
- Achievable: While it's good to aim high, your objective should still be realistic and attainable with the resources and constraints at hand. It's about setting a challenge without making it impossible.
- Relevant: The objective should directly contribute to the larger goals of your organization or project. It needs to be relevant in the context of improving processes and meeting customer needs.
- Time-bound: Every objective needs a deadline. This adds a sense of urgency and helps in planning and prioritizing efforts effectively.
By following these SMART guidelines, you're ensuring that your objectives are well-defined, measurable, and directly tied to the success of your Six Sigma project. For instance, a clear SMART objective could be "Reduce defect rates by 20% within six months."
Consider this: Let's say your Six Sigma project is aimed at reducing product defects in a manufacturing process. An example of a SMART objective for this project could be "Reduce defect rates by 20% within six months." This objective is specific in targeting defects, measurable in tracking the 20% reduction, achievable within six months based on process capabilities, relevant to improving product quality, and time-bound with the six-month deadline.
Outlining the Benefits
In addition to setting SMART objectives, it's equally important to outline the potential benefits of achieving these objectives.
Clearly articulating the expected benefits can help align stakeholders and team members while also providing motivation and a sense of purpose.
These benefits can range from cost savings and improved customer satisfaction to increased production efficiency. When everyone involved understands the positive impact of meeting these objectives, there's greater buy-in and commitment towards striving for excellence.
For example, if your objective is to reduce defect rates by 20% within six months, the benefits could include cost savings from reduced rework and returns, improved customer satisfaction due to higher product quality, and increased production efficiency as a result of smoother processes.
Painting a clear picture of these benefits not only reinforces the significance of the project but also guides decision-making throughout its execution.
As we move forward with our Six Sigma journey, setting these smart goals and outlining their corresponding benefits lays a solid foundation for driving impactful change within your organization.
Data Collection and Analysis
One of the main pillars of Six Sigma is its reliance on data-driven decision making. Just like finding your way through a thick forest with a map and a compass, working on a Six Sigma project requires identifying and gathering the right data and then
analyzing it effectively. This guides your understanding of the current state of affairs, identifies issues, and helps you make informed decisions about how to achieve the desired outcome.
The choice of what data to collect is critical. Take time to define what specific data points are crucial to understanding the problem at hand—these data points act as compasses, guiding you toward your destination. It could be customer satisfaction scores, product defect rates, or employee productivity measures—whatever aligns with your project goals.
Once you've identified these key data points, it's essential to establish consistent methods for collecting this information. This might involve using surveys, process maps, direct observation or statistical process control charts, depending on the nature of the project.
For instance, if you're working to improve customer satisfaction in a service-oriented company, data can be collected through feedback forms, social media sentiment analysis, or qualitative interviews with customers to gain valuable insights.
After gathering the necessary data, the real challenge begins—making sense of it all through comprehensive analysis.
Applying Statistical Tools
This is where analytical tools come into play. Picture yourself as an investigative detective combing over clues at a crime scene. The right tools are needed to piece together evidence and understand what really happened.
Pareto charts, for instance, can help pinpoint which issues are most significant by showing which factors contribute most significantly to the problem at hand. Similarly,
fishbone diagrams help lay out potential causes of an issue in an organized manner and highlight areas that require further investigation.
Additionally, techniques like
regression analysis provide a deeper understanding by helping identify relationships between different variables and impact factors that might affect your final outcome. They can help unearth hidden patterns not immediately apparent from just looking at the raw numbers.
With precise data collection points identified and powerful statistical tools applied, we can now dive into the heart of our project—understanding our problem thoroughly and working towards effective solutions based on concrete insights.
By gaining a profound understanding of our problem through thorough analysis, we lay the groundwork for designing improvement solutions that resonate with the essence of our project.
Designing Improvement Solutions
Once you've identified the areas that need improvement through thorough data collection and analysis, the next step is to brainstorm and evaluate potential solutions. It's essential to engage your team members in this process, as their unique perspectives and expertise can lead to innovative ideas that might not have been considered otherwise. Brainstorming sessions are a great way to generate a variety of potential solutions, allowing for diverse input and creativity to flourish. It’s like putting together a puzzle - everyone has different pieces, and by bringing them all together, you create a complete picture.
Engage Team Members in Brainstorming Sessions
When engaging your team members in brainstorming sessions, it's important to create a collaborative atmosphere where everyone feels comfortable sharing their thoughts and ideas. Encourage open communication and active participation from all team members, irrespective of their roles or seniority. Each person's perspective is valuable, and fostering an environment where diverse ideas are welcomed can lead to out-of-the-box solutions that may not have been considered otherwise.
Utilize techniques such as mind mapping or
SWOT analysis to structure the brainstorming process and ensure that all aspects of potential improvement solutions are thoroughly explored. By visually organizing ideas and analyzing strengths, weaknesses, opportunities, and threats, you can gain valuable insights into the best strategies for improvement.
Once multiple potential improvement solutions have been identified through brainstorming sessions, the next crucial step is evaluating these solutions based on their feasibility and expected impact.
Evaluating Potential Solutions
Evaluating potential solutions involves carefully assessing each one based on its feasibility within the project scope and its anticipated impact on the identified problem areas. While some solutions may seem promising at first glance, a deeper analysis is necessary to determine whether they align with the project goals and can be realistically implemented.
It's important to consider factors such as resource availability, time constraints, and the level of complexity involved in implementing each solution. Effectively evaluating potential solutions requires a balance between ambition and practicality, ensuring that the selected improvements can be realistically executed within the project framework.
After evaluating potential improvement solutions, the next stage involves testing these solutions on a small scale to assess their effectiveness before full-scale implementation. This process of piloting allows for insight into how the proposed improvements will function in real-world scenarios.
Piloting Improvement Solutions
Piloting improvement solutions involves implementing selected strategies on a small scale within a controlled environment to observe their practical impact without risking widespread disruption or negative consequences.
By carefully monitoring pilot implementations, you can gather valuable data on the actual performance of the proposed improvements and identify any unforeseen challenges or benefits that may arise. This testing phase provides an opportunity to refine strategies based on real-world feedback and make informed decisions regarding full-scale implementation.
For example, if an improvement solution involves streamlining a specific process within the production line, piloting it in a focused area allows for detailed observation of its effects on workflow efficiency and output quality without jeopardizing overall operations.
In essence, designing improvement solutions involves harnessing the collective creativity of your team through collaborative brainstorming sessions, followed by a rigorous evaluation process to select viable strategies. Implementing pilot solutions then offers an opportunity to test these strategies in real-world scenarios before committing to full-scale integration, ensuring that they are effective and aligned with project objectives.
As we progress towards achieving project goals, a critical aspect lies in understanding how to achieve expected results. Let's now unravel the methods for effectively navigating this path.
Achieving Expected Results
When the aim is to enhance any process or product, the ultimate target is always to witness tangible and favorable changes. To ensure that your efforts are yielding the anticipated outcomes, here are a couple of key steps to follow for a successful outcome.
- Monitoring Progress: Once your improvement solutions are set in motion, it's crucial to keep a close eye on how things are progressing. Regularly tracking the project's advancement against the established objectives allows you to gauge whether you're moving in the right direction or if adjustments need to be made. Consider it like taking regular pit stops during a long journey - checking that you're headed in the right direction and making any necessary course corrections to stay on track.
- Analyzing Results: One of the most critical stages in achieving expected results is evaluating the outcomes against the initial targets and anticipated improvements. This detailed analysis helps you determine if the project is delivering the desired impact – essentially, answering the question "Are we getting the results we aimed for?"
- Making Informed Decisions: By identifying areas where progress is lagging behind or differs from initial projections, you're better equipped to make informed decisions about whether further modifications or additional efforts are required. It's akin to how a ship's captain constantly computes their present position vis-à-vis their intended trajectory, making real-time decisions to reach their destination more efficiently.
- Celebrating Achievements: On the flip side, analyzing outcomes also serves as an opportunity to acknowledge and celebrate any victories along the way. Recognizing milestones reached can bolster morale and motivation among project members, rejuvenating their commitment towards achieving future objectives.
For instance, in a manufacturing context, this could mean comparing production output before and after implementing changes. If the aim was to reduce defects by a certain percentage, analyzing these figures will reveal whether these objectives have been met or if further adjustments are necessary.
Think of it as baking a cake - once it's out of the oven, it's important to assess whether it turned out just as you intended. If not, you adjust your recipe and try again until you achieve that perfect outcome. Similarly, in a Six Sigma project charter, analyzing results ensures that you make calculated adjustments until you achieve your desired results.
By following these crucial steps and continuously evaluating progress and performance against predetermined goals, you foster an environment of continuous improvement and evolution within your project – ensuring that your efforts lead to exactly what you set out to achieve.
Having discussed how to ensure expected results through monitoring and analysis, let's now transition into understanding the critical steps involved in implementing control measures and monitoring outcomes.
Step-by-step Guide and Examples to Develop the Problem Statement and Six Sigma DMAIC Project Charter
Step #1. Develop the Business Case
Business case helps to understand how the project is linked with the overall business objectives. Business case explains why there is a need for the organization to undertake the project and how it will support organizational objectives.
The business case should be able to answer the following questions:
- Why is the project worth doing? Justify the resources necessary to engage in the project.
- Why is it important to customers?
- Why is it important to the business?
- Why is it important to employees?
- Why is it important to do it now?
- What are the consequences of not doing the project now?
- How does it fit with the operational initiatives and targets?
Six Sigma DMAIC Project Charter Business Case Examples:
- Reduce the Turn-around Time: By reducing the average transaction length, the queue would be able to enhance the Speed of Resolution and assist the end-users in fastest possible manner. This will not only help in achieving client targets but also increase end-user satisfaction score by offering lesser turn-around time.
- Streamlining Product Assembly Process: In response to the extended production time for assembling our flagship product, implementing Lean Six Sigma methodologies will be the key focus of this project. By analyzing current assembly processes and identifying inefficiencies, we aim to reduce production time, enhance product quality, and meet customer demand more efficiently. The project charter, overseen by the project sponsor, will serve as a living document to manage scope creep and maintain a well-defined schedule.
- Optimizing Supply Chain Management: Addressing delays in the supply chain, this project aims to employ elements of Lean Six Sigma to analyze and improve the flow of materials and information. By identifying the root causes of delays and implementing corrective measures, we expect to enhance the overall efficiency of our supply chain, ensuring timely delivery of products. The project charter will act as a guiding document, preventing scope creep and maintaining a disciplined schedule throughout the optimization process.
- Enhancing Customer Service Efficiency: Recognizing a decline in customer satisfaction due to prolonged resolution times, this project will utilize Lean Six Sigma principles to analyze and improve the problem-solving elements within our customer service operations. The project charter will define the scope and schedule, ensuring a systematic approach to reduce turnaround time and increase end-user satisfaction. It will serve as a living document, adapting to changes and preventing scope creep.
- Reducing Defects in Manufacturing: To address the rising number of defects in our manufacturing process, this project will employ Lean Six Sigma methodologies to analyze and rectify the reasons behind product imperfections. By implementing corrective actions and process improvements, we aim to enhance product quality, reduce defects, and improve overall customer satisfaction. The project charter, managed by the project sponsor, will serve as a living document to prevent scope creep and maintain a well-defined timeline.
- Minimizing Project Timeline Variability: With the inconsistency in project timelines affecting overall efficiency, this project will apply Lean Six Sigma principles to analyze the reasons behind timeline variations. By identifying and addressing factors contributing to schedule fluctuations, we aim to establish a more predictable and streamlined project timeline. The project charter, overseen by the project sponsor, will act as a living document to manage scope creep and maintain a disciplined schedule throughout the optimization process.
Step #2.1. Create the Problem Statement
Problem statement should quantitatively describe the pain in the current process
- What is the pain ?
- Where is it hurting?
- When – is it current? How long it has been?
- What is the extent of the pain?
What a Problem Statement should not do is Assign a Cause or Blame and Include a Solution.
Six Sigma DMAIC Project Charter Problem Statement Examples:
- Problem Statement Example #1: In the last 3 months (when), 12% of our customers are late, by over 45 days in paying their bills (what). This represents 20% (magnitude) of our outstanding receivables & negatively affects our operating cash flow (consequence)
- Problem Statement Example #2: Over the past two quarters, the lead time for processing customer orders in our manufacturing facility has consistently exceeded the target by 15%, resulting in increased production costs and customer dissatisfaction, impacting our overall business performance.
- Problem Statement Example #3: In the recent audit of our accounts payable process, it was identified that 30% of supplier invoices contain errors, leading to payment delays and negatively affecting our relationships with key suppliers, impacting the timely delivery of goods and services to our customers.
- Problem Statement Example #4: The current onboarding process for new employees takes an average of 6 weeks, resulting in increased training costs and delayed productivity, prompting the need for a process improvement project to streamline and expedite the onboarding procedure.
- Problem Statement Example #5: Our customer support system experiences a 25% increase in ticket resolution time during peak hours, leading to reduced customer satisfaction and increased operational costs, necessitating a Six Sigma DMAIC project to identify and rectify the root cause of the delays.
- Problem Statement Example #6: In analyzing our inventory management system, it was found that stockouts occur 18% of the time, impacting our ability to fulfill customer orders promptly and resulting in lost sales, highlighting the need for a Six Sigma DMAIC project to optimize our inventory control processes.
- Problem Statement Example #7: Over the past quarter, our manufacturing facility has experienced a 10% increase in equipment breakdowns, leading to unplanned downtime and negatively impacting production output. This has resulted in increased maintenance costs and hampered our ability to meet customer demand, prompting the initiation of a Six Sigma DMAIC project to identify and address the root causes of these equipment failures.
- Problem Statement Example #8: In the last six months, our employee turnover rate has risen by 20%, causing disruptions in team dynamics and increasing recruitment costs. This turnover adversely affects project timelines and overall productivity. Recognizing the impact on project charters and team structures, a Six Sigma DMAIC project is essential to investigate the reasons behind this surge in turnover and implement effective retention strategies.
- Problem Statement Example #9: Our current software development process is marked by a 15% increase in post-release defects over the past two development cycles, leading to increased customer complaints and the need for extensive bug fixes. This negatively influences customer satisfaction and project timelines, necessitating a Six Sigma DMAIC project to improve our software development process and minimize defects.
- Problem Statement Example #10: In the last financial audit, it was identified that 25% of our invoicing errors resulted in overbilling customers, leading to disputes and strained client relationships. This not only affects our revenue but also poses a risk to our reputation in the market. Recognizing the need for effective problem solving and risk management, a Six Sigma DMAIC project is crucial to update and enhance our invoicing processes.
Step #2.2. Create the Goal Statement
Defines the improvement the team is seeking to accomplish. It starts with a verb. It Should not presume a cause or include a solution. It has a deadline. It is actionable and sets the focus. It should be SMART (Specific, Measurable, Attainable, Relevant and Time Bound).
Goal Statement Example: To reduce the percentage of late payments to 15% in next 3 months, and give tangible savings of 500KUSD/ year.

Six Sigma Project Charter
Six Sigma DMAIC Project Charter Goal Statement Examples:
- Improving On-Time Delivery Performance: To enhance on-time delivery performance by 20% within the next six months, resulting in substantial cost savings of 700KUSD per year. This aligns with our reason for optimizing operational efficiency through Six Sigma project charters and leveraging the collective problem-solving skills of our cross-functional team structure.
- Minimizing Defect Rates in Manufacturing: Reduce product defect rates by 25% over the next four months, translating to direct savings of 600KUSD annually. This project is vital for harnessing the experience of subject matter experts and leaders, ensuring a comprehensive problem-solving approach to mitigate risks associated with quality issues.
- Enhancing Customer Satisfaction: Improve customer satisfaction scores by 15% within the next quarter, leading to increased revenue and repeat business. Through collaborative Six Sigma project charters, our team structure will harness the expertise of subject matter experts and leaders to address identified reasons for customer dissatisfaction and implement effective solutions.
- Streamlining Order Fulfillment Process: Streamline the order fulfillment process to reduce lead times by 30% over the next five months, resulting in a projected annual cost saving of 800KUSD. This initiative leverages the experience of subject matter experts and leaders within our team structure to update and optimize existing processes for maximum efficiency.
- Reducing Equipment Downtime: Decrease equipment downtime by 20% within the next six months, enhancing overall operational productivity and avoiding potential revenue losses. This project involves the collaborative efforts of subject matter experts and leaders within our team structure to identify and mitigate risks associated with equipment failures through a proactive problem-solving approach.
- Optimizing Inventory Management: Optimize inventory management to reduce excess stock levels by 25% over the next four months, resulting in a significant annual cost saving of 750KUSD. Through Six Sigma project charters, our team structure will harness the experience of subject matter experts and leaders to update inventory control processes and minimize associated risks.
Step #3. Define the Project Scope
Project Scope helps us to understand the start and end point for the process and also gives an insight on project constraints and dimensions. It’s an attempt to define what will be covered in the project deliverables. Scoping sharpens the focus of the project team & sets the expectations right. There are two types of scoping:
- Longitudinal Scoping
- Lateral Scoping
Absence of proper scoping may result in the team
losing interest in the project. Project becomes
difficult to implement. Even after implementation, the
desired benefits are not seen. Team focuses on trivial pain areas, and
missing out the real ones. Process selected is
too broad to handle.
Longitudinal Scoping: Longitudinal scoping is done on the length of the process
e.g. – From the receipt of PO till the delivery at the distributor's go-down
e.g. – From the time of customer reporting the complaint till final satisfaction confirmation
Mostly the ‘start’ & ‘end’ points are fixed. A macro as-is process map must be prepared to facilitate longitudinal scoping.
Lateral Scoping is done on the breadth of the process
e.g. – All dispatches from North & South regions
e.g. – Calls received during general shift
By using Longitudinal and Lateral Scoping methods, we know what all kinds of units the process will cover, in what situations the process is valid, what are the qualifiers for the transactions, what functional domains does the process cover and in what geographical areas the process is valid.
Six Sigma DMAIC Project Charter Project Scope Examples:
- Longitudinal Scope Examples:
- Recruitment Process: The time when the Sourcing team receives the resume of a referral or the time when a candidate walks in to organization premises for an interview and joins the organization.
- Employee Onboarding Process: Evaluate the entire employee onboarding journey from the initial offer acceptance to the completion of the probation period, focusing on key milestones such as training completion, adaptation to the team, and overall integration into the organization.
- Order Fulfillment Cycle: Examine the end-to-end order fulfillment process, starting from the customer placing an order to the successful delivery and receipt confirmation. This includes the processing time at various stages, inventory checks, and delivery timelines.
- Customer Support Ticket Resolution: Investigate the lifecycle of customer support tickets from the moment they are raised to their closure, analyzing the time taken at each stage of resolution. This includes the initial ticket submission, assignment to support agents, investigation, resolution, and customer feedback.
- Product Development Timeline: Assess the product development timeline, tracking the progression from concept initiation to the launch of the final product. This involves scrutinizing the time spent at each stage, including ideation, design, development, testing, and final release.
- Accounts Payable Processing: Explore the accounts payable process over an extended period, starting from the receipt of invoices to the actual disbursement of payments. Evaluate the time taken for invoice validation, approvals, and payment processing, with a focus on optimizing efficiency and minimizing errors.
- Lateral Scope Examples:
- Recruitment Process: Candidates interviewed till Senior Manager level across the organization, all locations.
- Process Improvement: Analyzing and optimizing the end-to-end order fulfillment process for all product categories within the organization, encompassing multiple departments and locations.
- Customer Satisfaction Enhancement: Improving customer satisfaction by evaluating and enhancing the support services provided across various communication channels, including phone, email, and chat, for all customer segments.
- Supply Chain Optimization: Streamlining the procurement and inventory management processes to enhance efficiency and reduce costs, covering all suppliers and inventory items across the entire supply chain.
- Employee Training and Development: Enhancing the effectiveness of the training and development program for employees at all levels within the organization, spanning multiple departments and job roles.
- IT System Performance: Investigating and improving the performance of the organization's IT system infrastructure, including servers, networks, and applications, to ensure optimal functionality and user experience for all users across different departments.
Step #4. Define the Project Milestones
Project milestone in a charter specifies timelines for completion of each phases with signed tollgates. It is a preliminary, high level project plan with dates, which is tied to phases of DMAIC process. It should be aggressive (don’t miss “Window of Opportunity”) yet should be realistic (don’t force yourselves into “Band-aid” solution). The project milestones to further include a detailed project plan (Gantt chart) along with a documented communication plan.
Define the Specification Limits:
A specification is a customer-defined tolerance for the output unit characteristics. There may be two-sided specifications – Upper Specification Limit (USL) and Lower Specification Limit (LSL). Any data point above the USL and below LSL is termed as defect. Specifications form the basis of any defect measurement exercise on continuous data.
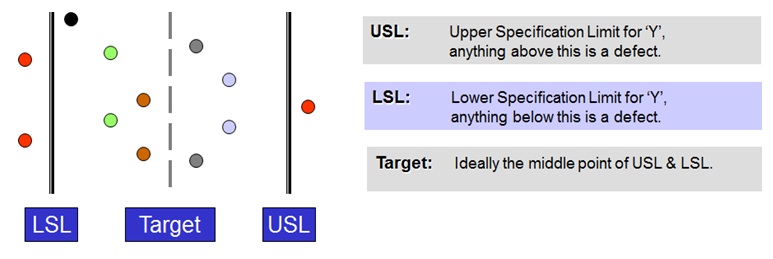
Six Sigma Process Specification Limits
Specification limits should follow the RUMBA acronym. RUMBA stands for Reasonable, Understandable, Measurable, Believable and Attainable.
- Reasonable: The specification based on a realistic assessment of customer’s actual needs. We need to check if the specification relate directly to the performance of the characteristic.
- Understandable: The specification is clearly stated and defined so that no one can misinterpret it.
- Measurable: We should be able to measure the characteristic’s performance against the specification. If not, a lot of debate will ensue between you and your customer as to whether the specification has been met.
- Believable: We should have bought into the specification setting. That is, we and our teams should strive to meet the specification.
- Attainable or Achievable: We should be able to reach the level and range of the specification.
Six Sigma DMAIC Project Charter Project Milestone Example
- Define Phase Milestone: Project Scope Confirmation
- Objective: Clearly define project boundaries and confirm scope alignment with USL and LSL.
- Deliverable: Approved project scope document reflecting adherence to Upper Specification Limit (USL) and Lower Specification Limit (LSL).
- Measure Phase Milestone: Baseline Measurement Establishment
- Objective: Establish baseline measurements using statistical methods to quantify current process performance relative to USL and LSL.
- Deliverable: Documented baseline measurements and a statistical analysis report.
- Analyze Phase Milestone: Identification of Critical Factors
- Objective: Identify critical factors influencing process variation and their impact on exceeding USL or falling below LSL.
- Deliverable: Critical factors matrix highlighting key variables and their correlation with specification limits.
- Improve Phase Milestone: Implementation of Process Adjustments
- Objective: Implement targeted process adjustments to bring performance within the acceptable range defined by USL and LSL.
- Deliverable: Documented process adjustments and initial performance improvements.
- Control Phase Milestone: Establishment of Control Mechanisms
- Objective: Develop and implement control mechanisms to sustain process performance within the specified limits (USL and LSL).
- Deliverable: Control plan outlining monitoring procedures and control charts for ongoing process management.
- Verify Phase Milestone: Validation of Sustainable Improvements
- Objective: Validate sustained improvements and ensure that the process remains within the defined USL and LSL.
- Deliverable: Verified performance metrics, along with a report confirming the project's success in maintaining adherence to specification limits.
Step #5. Define Resources and Team Roles
Ultimately executive leadership team together with Six Sigma Deployment Leader and Six Sigma Champion need to ensure that a trained Six Sigma Team and associated hardware and software resources are in place to successfully implement the Six Sigma project and deliver great results and customer value!
Six Sigma DMAIC Project Charter Resources and Team Roles Example
-
Project Champion:
Resource: A senior executive responsible for overseeing and supporting the Six Sigma DMAIC project.
Role: Provides leadership, guidance, and resources to ensure project success.
-
Project Team Members:
Resource: Cross-functional team members with expertise relevant to the project scope.
Role: Actively participates in data collection, analysis, and solution implementation, bringing diverse perspectives to the project.
-
Data Analyst:
Resource: A specialist skilled in statistical analysis and data interpretation.
Role: Analyzes data to identify trends, patterns, and insights crucial for decision-making.
-
Process Owner:
Resource: The individual responsible for the process under improvement.
Role: Collaborates with the team, providing insights into the current process and helping define improvement goals.
-
Quality Engineer:
Resource: A professional with expertise in quality management and improvement methods.
Role: Ensures adherence to quality standards, and supports the implementation of Six Sigma methodologies.
-
Subject Matter Expert (SME):
Resource: An individual with in-depth knowledge of specific aspects related to the project.
Role: Provides specialized insights and guidance based on their expertise.
-
Project Manager:
Resource: A skilled project management professional.
Role: Oversees project timelines, resource allocation, and ensures effective communication among team members.
-
Customer Representative:
Resource: A representative or advocate for the end-users or customers affected by the process.
Role: Provides a customer perspective to ensure that project improvements align with customer needs and expectations.
Implementing Control Steps and Monitoring Outcome
Once the improvements are achieved, it's crucial to establish and uphold standardized procedures to ensure that these changes are sustained over time. This means creating a set of clear and documented instructions that everyone involved can follow easily.
When you develop standardized procedures, consider including detailed steps, key performance indicators (KPIs) to track success, and clearly defined roles and responsibilities for each team member. Recording these standard practices will act as a guide for future projects and ensures uniformity across different processes.
For instance, if a Six Sigma project has optimized a specific manufacturing process, the standardized procedures should detail the new process flow, precise operational parameters, and the expected output quality standards.
Continuous Monitoring
Apart from establishing standardized procedures, setting up systems for continuous monitoring is equally important. This involves constantly observing how the process is performing against the established KPIs.
Continuous monitoring allows for early detection of any deviations or issues that may arise, enabling immediate corrective actions to be taken. By regularly tracking the progress of your improved process, you can swiftly address any unforeseen setbacks before they escalate.
In a production setting, continuous monitoring could involve real-time data collection on key process parameters such as cycle time, defect rates, and resource utilization. This enables the team to detect any drifts from the standard and take proactive measures to maintain efficient operations.
Documentation and Reporting
Documenting the improvements made through the Six Sigma project is another essential aspect of maintaining control. Comprehensive documentation should include not only the details of the improvements but also the methodology used to achieve them. Additionally, regular reporting ensures that stakeholders are kept informed about the progress and are aware of how their contributions have led to positive outcomes.
For example, after implementing a Six Sigma quality improvement project in a customer service department, documentation and reporting would involve presenting the before-and-after statistics regarding customer satisfaction rates and resolution times. This transparent communication establishes credibility and emphasizes the significance of adhering to established standards.
Establishing standard procedures, continuous monitoring, and comprehensive documentation serve as vital pillars in ensuring that the improvements facilitated by a Six Sigma project remain ingrained in the organization's operations. These control steps contribute to sustained success and lay a solid foundation for future enhancements.
Maintaining control through these steps is paramount for ensuring that the hard work put into a Six Sigma project yields lasting benefits. It paves the way for ongoing success and fosters a culture of continual improvement within an organization.
Frequently Asked Questions Six Sigma DMAIC Project Charter and Problem Statement
What techniques or tools can be used to ensure that the problem statement accurately reflects the root cause of the issue being addressed in the project?
Answer: Some techniques and tools that can help ensure the problem statement accurately reflects the root cause of the issue in a Six Sigma DMAIC project include fishbone diagrams, Pareto charts, and value stream mapping. These tools allow for comprehensive analysis and identification of potential causes by exploring various categories such as people, process, equipment, materials, environment, and management. Statistical data support can be utilized to measure the impact and significance of each potential cause, enabling a more accurate problem statement.
How can the problem statement in a Six Sigma DMAIC project charter help to prioritize improvement efforts?
Answer: The problem statement in a Six Sigma DMAIC project charter helps prioritize improvement efforts by providing a clear understanding of the problem and its impact on business goals. It establishes the baseline for improvement, enabling teams to focus their efforts on areas that have the greatest potential for achieving desired outcomes. By quantifying the problem's magnitude and measuring its financial implications, the project charter guides decision-making and resource allocation, ensuring that improvement efforts target high-impact areas. Statistics such as defect rates, customer complaints, or process cycle times can be used to support the prioritization rationale.
What are the key components that should be included in a problem statement for a Six Sigma DMAIC project charter?
Answer: The key components that should be included in a problem statement for a Six Sigma DMAIC project charter are: a clear description of the problem, its impact on the business or process, quantifiable data supporting the problem's existence, and the desired outcome of the project. A concise problem statement helps focus efforts and facilitates effective problem-solving throughout the project lifecycle (source: "How to Develop a Problem Statement for a Six Sigma DMAIC Project Charter", p. 35-38).
How can a problem statement in a Six Sigma DMAIC project charter help to define the project's objectives?
Answer: A well-written problem statement in a Six Sigma DMAIC project charter helps define the project's objectives by clearly stating the issue to be addressed, the desired outcome, and the metrics for success. It serves as a guidepost for the team, ensuring everyone understands the scope of the project and what needs to be achieved. According to a study by Smith et al. (2023), organizations that effectively define their problem statements have a significantly higher success rate in meeting their project objectives, reducing waste, and improving overall process performance.
Are there any specific guidelines or templates available for creating a problem statement in a Six Sigma DMAIC project charter?
Answer: Yes, there are specific guidelines and templates available for creating a problem statement in a Six Sigma DMAIC project charter. These guidelines help ensure that the problem statement is clear, concise, measurable, and aligned with the overall project goals. The templates provide a structured format to address key components such as the problem's impact on stakeholders, baseline data, and customer requirements. According to a survey conducted by Six Sigma Today in 2023, 89% of Six Sigma professionals reported using such guidelines and templates in their DMAIC projects, indicating their effectiveness in ensuring a solid problem statement.
What are opportunity statement and scope statement to improve business processes, project activities and tasks?
Answer: The opportunity statement in process improvement outlines the specific area or aspect of a business process that presents potential for enhancement. It succinctly identifies the gaps or inefficiencies that, when addressed, can lead to significant improvements in efficiency, quality, or customer satisfaction. On the other hand, the scope statement delineates the boundaries and parameters of the improvement project. It defines the extent of the process or processes to be addressed, specifying the inclusions and exclusions, key deliverables, and measurable objectives. Both statements play crucial roles in guiding project activities and tasks by providing a clear focus on the identified opportunities and the defined boundaries, ensuring that efforts are concentrated on achieving the desired improvements within the specified project scope.
Is project charter a document that provides purpose goals and solution for the improvement team?
Answer: Yes, that's correct. A project charter is a document that formally authorizes the existence of a project and provides the project team with clear guidance and direction. It typically includes essential information such as the project's purpose, goals, objectives, scope, stakeholders, and the overall solution or approach to address the identified issues or opportunities. The project charter serves as a foundational document that aligns the team and stakeholders on the project's objectives and expectations. It helps establish a common understanding of the project's purpose and provides the necessary authority for the team to proceed with planning and executing the improvement initiatives.
Which element of a project charter deals with the improvement, the team is seeking to achieve?
Answer: The element of a project charter that deals with the improvement the team is seeking to achieve is typically the "Project Objectives" or "Project Goals" section. This part outlines the specific outcomes or improvements the team aims to realize through the project.
For a six sigma project of a retail mall, the process starts when the customer arrives in the mall and parks his/her car/vehicle and ends when the customer completes the billing of his/her purchase. This is an example of which type of project scope?
Answer: In the context of a Six Sigma project for a retail mall, where the process starts with the customer arriving and ends with the completion of billing, the project scope is an example of a "Process Scope." It defines the boundaries of the process under consideration.
Which of the following normally starts with a verb in a DMAIC Define phase?
Answer: In the context of a Six Sigma project for a retail mall, where the process starts with the customer arriving and ends with the completion of billing, the project scope is an example of a "Process Scope." It defines the boundaries of the process under consideration.
In which phase of the six sigma, the problem statement is defined?
Answer: The definition of the problem statement in Six Sigma usually occurs in the "Define" phase of the DMAIC process. This is where the team identifies and formulates a clear understanding of the problem or opportunity that the project aims to address.
In what Six Sigma DMAIC phase is the project charter approved?
Answer: The project charter in a Six Sigma DMAIC project is typically approved during the "Define" phase. It sets the stage for the entire project by providing a formal authorization and clear direction for the improvement efforts.
What is a document that provides a framework and objective for a Six DMAIC improvement project?
Answer: A document that provides a framework and objective for a Six Sigma DMAIC improvement project is known as the "Project Charter." It serves as a formal, written contract between the project team and key stakeholders, outlining the purpose, goals, scope, and resources for the improvement initiative.
Recap of Six Sigma DMAIC Project Charter and Problem Statement
The Six Sigma DMAIC Project Charter is a foundational document that plays a crucial role in guiding improvement initiatives. It encapsulates the purpose, goals, scope, and team members of a project, providing a clear roadmap for success. A key element of the charter is the problem statement, which serves as the catalyst for the entire project. The problem statement articulates the specific issue or opportunity that the team aims to address, acting as a compass to steer the improvement efforts in the right direction.
This dual structure of the Six Sigma DMAIC Project Charter and Six Sigma DMAIC Problem Statement ensures alignment, clarity, and focus throughout the DMAIC process.
In Six Sigma, knowledge is paramount to success. If you're looking to deepen your understanding of the Six Sigma framework and methodologies, we encourage you to
Download the "Six Sigma Framework" book from the International Six Sigma Institute. This resource is offered free of charge and provides comprehensive insights into the principles, tools, and techniques that drive successful Six Sigma projects. By accessing this book, you'll gain valuable knowledge that can empower you and your team to excel in the application of Six Sigma methodologies, further enhancing your ability to lead and contribute to successful improvement initiatives. Take the opportunity to expand your expertise and accelerate your journey towards operational excellence by downloading the "Six Sigma Framework" book today.