Out of Control Processes (SPC) Identified by Control Charts
Identifying and Managing SPC Out of Control Processes
With a process control chart, you can keep track of your manufacturing process as it changes over time. It gives you a picture of the average, as well as the upper and lower limits of the process - these are clues to know if things are going right or wrong. But it's more than just watching for points that fall outside these limits. You also need to look at repeated patterns or too many points on one side; these signs suggest something unusual is happening with your process. Now you're ready to start exploring out-of-control processes.
Using a process control chart, you can monitor your process's variation over time by identifying out-of-control signals such as points outside the control limits, runs of points on one side of the centerline, or consistent patterns. By analyzing these signals and investigating their causes, you can effectively bring your process back under control and ensure consistent quality in your operations.
Fundamentals of Out of Control Process Control Chart
To comprehend an out-of-control process control chart, it's crucial to grasp its primary purpose. A control chart vividly displays the changes in a manufacturing process over time, which is pivotal for ensuring consistent quality output. It does this by plotting data points in time order, giving a visual representation of how the process behaves over time. The centerline of the chart represents the average performance, while the upper and lower control limits provide a boundary of acceptable variation.
The upper and lower control limits are not arbitrary values; rather, they are determined from historical data that represents the inherent variability within the process. By establishing these limits, the chart offers a clear reference point for distinguishing between normal, predictable variation and exceptional, unpredictable variations that signal an out-of-control process.
In essence, control charts act as a reliable diagnostic tool for identifying variations beyond what is considered typical for the given process. This is crucial because it allows manufacturers to distinguish between common cause variation – which is expected and inherent to the process – and special cause variation – which occurs less frequently and signifies that something unusual has affected the normal operation of the process.
These limits are established from historical data and help to identify if there are consistent or unpredictable variations in the process.
By honing in on these variations, businesses can make informed decisions about whether adjustments need to be made to ensure that their processes remain in control and products consistently meet quality standards. This proactive approach not only enables timely corrective actions but also supports continuous improvement initiatives aimed at enhancing overall productivity and efficiency within the manufacturing environment.
Having laid the foundation for understanding the importance of an out-of-control process control chart, we'll now explore in more depth how these charts assist in managing and mitigating unforeseen process variations, ensuring consistent product quality.
What is the Out of Control Process?
A process is said to be out of control if you identify one or more of the following symptoms in its process control chart:
- One or more data points fall outside the control limits.
- Seven consecutive data points increasing or decreasing.
- Eight consecutive data points are on one side of average.
- Fourteen consecutive data points alternating up & down.
- Two data points, out of three consecutive data points, are on the same side of the average in zone A or beyond.
- Four data points, out of five consecutive data points, are on the same side of the average in zone B or beyond.
- Fifteen consecutive data points are within zone C (above and below the average).
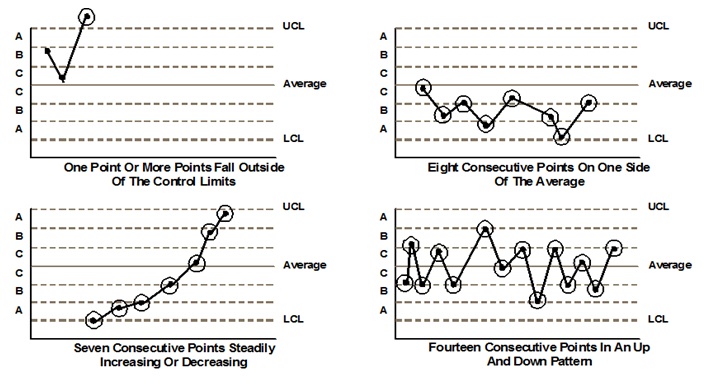
Six Sigma Out of Control Charts-1
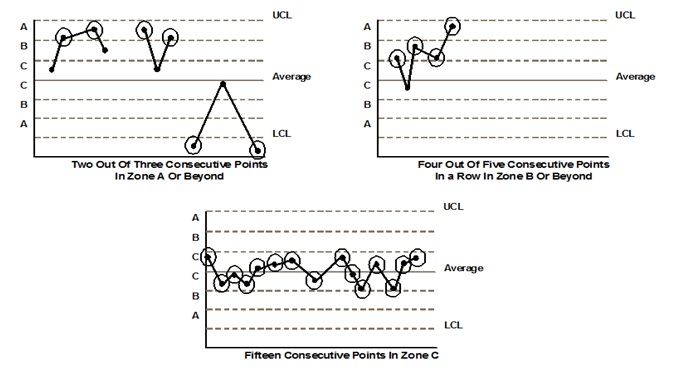
Six Sigma Out of Control Charts-2
Identification Methods of Out of Control Processes
In identifying out-of-control processes using control charts, there are a few key indicators to consider. These act as signals alerting us when something goes awry with our process – perhaps due to machine malfunctions or operational errors.
One of the most obvious signs is
points outside the control limits. If you notice points crossing these lines on your chart, it's a clear indication that something unusual is happening and immediate attention is warranted.
Another important signal is successive points on one side of the centerline beyond certain thresholds. This suggests a consistent shift or trend in performance, allowing for the identification of specific changes that have occurred. Analogous to transitioning seasons, just as successive days of cooler weather indicate a shift from summer to fall, in manufacturing, this kind of pattern may signal process drift.
It's also critical to look for
runs of points on one side of the centerline. This indicates whether the process has consistently underperformed or overperformed compared to its usual behavior. For instance, if a machine begins consistently producing low-quality products due to deviation from its standard operation, this pattern would be evident on the control chart.
These signals serve as red flags, prompting us to closely monitor our manufacturing process. By understanding these methods and staying alert for these signals, we can detect deviations early and take corrective action before major issues arise.
Armed with an understanding of identification methods for out-of-control processes, we now turn our attention to exploring unique scenarios that require special consideration in process management.
What is SPC (Statistical Process Control)?
Statistical Process Control (SPC) is a systematic method employed in various industries to monitor, control, and enhance processes. This method relies on the analysis of measurements and attribute data to ensure that a process operates efficiently and consistently over time. SPC utilizes control charts, graphical representations that display the variation in a process and highlight any deviations from the norm. These charts typically include control limits, namely the Upper Control Limit (UCL) and Lower Control Limit (LCL), which serve as thresholds for acceptable variation. By plotting measurements or attribute results on these charts, organizations can quickly identify patterns, trends, or anomalies that may indicate an out-of-control process.
The control limits in SPC act as crucial indicators, guiding decision-makers in understanding whether a process is operating within acceptable parameters. The UCL and LCL provide a visual representation of the expected range of variation, helping teams distinguish between common cause variation, which is inherent in the process, and special cause variation, which signifies an anomaly or unexpected occurrence. Through regular monitoring of control charts, organizations can gather valuable information about the stability and performance of their processes. The graphical representation aids in the efficient interpretation of data, allowing for timely interventions to address any deviations and maintain control over the overall process.
Effective implementation of Statistical Process Control not only aids in identifying out-of-control processes but also facilitates proactive management of these deviations. By relying on accurate measurements and attribute data, organizations can make informed decisions to optimize processes, minimize defects, and enhance overall efficiency. SPC serves as a powerful tool in continuous improvement efforts, enabling teams to focus on root causes of variation and implement targeted solutions. This method transforms raw data into actionable insights, fostering a culture of data-driven decision-making and ensuring that processes remain within defined control limits. Ultimately, the integration of SPC into organizational practices empowers teams to achieve consistent and high-quality results.
How to identify and analyze out-of-control points on an SPC chart?
In Statistical Process Control (SPC), recognizing and scrutinizing out-of-control points on an SPC chart is pivotal for maintaining quality standards. The specification limits, denoting the acceptable range of variation, serve as a compass in this journey. An out-of-control point signals a deviation beyond these predefined boundaries, acting as an index of potential issues within the system. Identifying the source of such anomalies demands a comprehensive analysis of the sample data and applying statistical methods to unveil patterns or trends. By leveraging statistical tools and techniques, practitioners can systematically navigate through the intricacies of the process, ensuring effective management of out-of-control occurrences and fortifying the overall quality of the system.
What actions should I take when my SPC chart shows signs of instability?
When confronted with signs of instability on an SPC chart, the initial step is to thoroughly analyze the sources of process variation. Examine the collected samples and scrutinize the statistics to identify patterns or anomalies within the distribution. A meticulous evaluation of these elements is essential for pinpointing the root causes behind the out-of-control processes. Once the sources of instability are discerned, strategic measures can be implemented to manage and rectify the identified issues, thereby restoring the control of the process and ensuring the sustained reliability of the system.
Can I still salvage a process that has gone out of control?
Certainly, the capability to salvage a process that has gone out of control largely depends on the timely identification of the root causes and the implementation of effective corrective actions. When a process deviates from its established control limits, it indicates a departure from its normal operating conditions. The first step is to thoroughly investigate the factors contributing to the out-of-control state. This involves a comprehensive analysis of the collected data, samples, and statistical indicators to pinpoint sources of variation. Once these sources are identified, swift and targeted interventions can be executed to address the underlying issues and restore the process to a controlled state.
However, the success of salvaging a process also hinges on the organization's responsiveness and adaptability. Proactive measures such as continuous monitoring, regular audits, and a robust quality management system contribute to early detection of potential deviations, minimizing the impact and increasing the likelihood of successful recovery. Effective communication and collaboration among teams are equally vital in swiftly implementing corrective actions. In essence, while salvaging an out-of-control process is feasible, it demands a proactive and systematic approach to problem-solving and continuous improvement within the organization.
Examination of Special Case Scenarios
Every manufacturing process has its unique characteristics, leading to many unusual situations or signals that may cause the process to deviate from its normal behavior.
One of the more common abnormal scenarios is equipment malfunctions causing sudden spikes or dips in production output, resulting in irregular data points on the control chart. Addressing these issues immediately is imperative to bring the process back under control, preventing significant quality issues and production delays.
Additionally, issues with material quality can trigger out-of-control signals on a process control chart. Close collaboration with suppliers is crucial to ensure consistent material quality and avert variations that could disrupt the manufacturing process.
An instance could be a batch of steel used in automotive part manufacturing containing impurities or inconsistencies, leading to increased defect rates or fluctuations in product dimensions, both triggering out-of-control signals on the control chart.
Successfully managing such special case scenarios requires not only proactive problem-solving but also ongoing collaboration with all stakeholders involved in the manufacturing process. By carefully examining and addressing these unique instances, a company can maintain stable production processes and uphold high-quality standards.
With a clear understanding of how special case scenarios impact manufacturing processes, it's time to consider implementing control process rules for effective management and, ultimately, improvement.
Implementation of Control Process Rules
In manufacturing, processes can be complex and sensitive, involving numerous steps and variables. This is where control process rules come in; they provide a systematic and methodical way of detecting when a process is out of control, allowing for timely intervention and correction. Two well-known sets of control process rules are the
Western Electric Rules and the
Nelson Rules.
Western Electric Rules are prominently used to identify when a process is out of control by using a series of criteria related to the number and pattern of data points plotted on the control chart. These rules give clear guidelines for detecting specific signals that indicate an out-of-control process, such as points outside the control limits, runs beyond certain thresholds, or consistent patterns.
On the other hand, the
Nelson Rules offer a different set of criteria for identifying out-of-control processes. They focus on specific patterns and trends in data over time, giving manufacturers additional tools to recognize variability and inconsistency in their processes.
These rules are not just arbitrary instructions but are based on statistical measures and techniques that have been refined over time through extensive research and practice in the manufacturing industry.
Imagine these control process rules as your internal quality assurance team – constantly monitoring and analyzing every aspect of your manufacturing process to ensure that it stays within acceptable limits. By strictly following these rules, organizations can maintain consistency in their products while promptly addressing any irregularities that may arise.
Furthermore, having clear and predefined rules allows for objective decision-making within an organization. When deviations from these rules occur, it triggers an investigation into the root cause and necessitates corrective action.
Strict adherence to these control process rules provides a robust framework for maintaining product quality in manufacturing processes, thereby gaining customer trust and confidence.
We've now seen how essential implementing control process rules can be in ensuring the consistent quality of manufactured products. Let's explore how these rules can impact overall productivity and profitability in manufacturing environments.
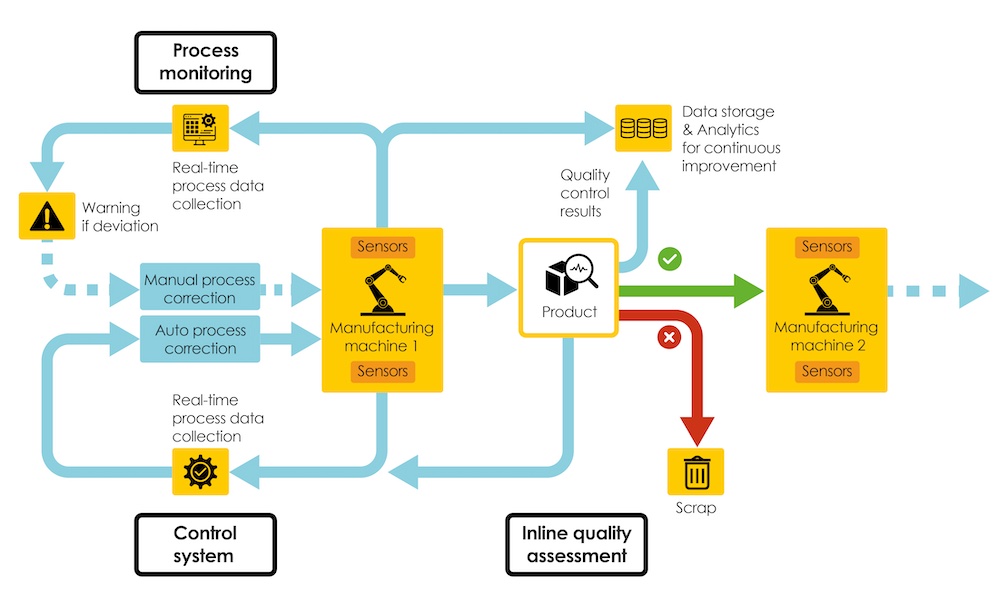
Six Sigma DMAIC Out Of Control Process Detection
Evaluating Importance of Rule Violations
When a control process rule is violated, it's not just a small mistake. Understanding these violations' seriousness is crucial because they can have far-reaching consequences, affecting everything from the final product's quality to the safety of workers and consumers. This assessment plays a critical role in maintaining consistency in manufacturing processes and upholding product quality standards.
A Comparative Analysis
One way to estimate the significance of a rule violation is by conducting a comparative analysis of different types of violations to understand their frequency and impact on production output. By comparing the frequency and impact of various rule violations, manufacturers can prioritize their corrective actions based on the potential risk associated with each type of violation.
Statistical Comparison
In addition to understanding the frequency and impact, it's crucial to conduct a statistical comparison of the cost implications of different rule violations. This involves quantifying the financial impact of each violation on production costs, waste management, rework, and potential regulatory fines. Such statistical comparisons provide tangible data for decision-making regarding corrective actions.
Time Implications
Furthermore, evaluating the time required to rectify different types of rule violations is essential. Manufacturers need to analyze how long it takes to identify, address, and correct various types of violations. This analysis helps in resource allocation and process optimization, ultimately contributing to improved efficiency.
Safety Impact
Another vital aspect of evaluating rule violations is analyzing their safety implications. Different violations can pose varying degrees of risk to the safety and well-being of workers and end consumers. Understanding these safety implications allows manufacturers to prioritize corrective actions that mitigate potential hazards.
Customer Impact
It's also important to analyze the customer impact of various rule violations. Quality deviations can lead to dissatisfaction among customers, impacting brand reputation and customer loyalty. By quantifying the effect of different violations on customer satisfaction, manufacturers can tailor their corrective measures to align with customer expectations.
By conducting a comprehensive evaluation of rule violations across these dimensions, manufacturers gain valuable insights into the critical areas that require attention and corrective measures. This not only aids in bringing processes back into control but also paves the way for continuous improvement and sustained product quality excellence.
With a clear understanding of the critical aspects involved in evaluating rule violations, let's now shift our focus to exploring advanced techniques for analyzing process control data.
Analysis Techniques for Process Control Data
When it comes to handling process control data, statistical techniques play a critical role in understanding the performance and stability of manufacturing processes. Let's explore some key analysis methods that provide valuable insights.
Statistical Calculations
Statistical calculations form the bedrock of process control data analysis. One essential metric is
standard deviation, which measures how much variation there is from the average. By analyzing this variation, manufacturers can understand if their process is consistent or unpredictable, pinpointing areas that may require improvement.
Another key technique is
process capability analysis, which evaluates the ability of a process to meet specified requirements. This tool enables organizations to compare their current process capabilities with customer requirements and make informed decisions on process enhancements.
Trend Analysis
Trend analysis involves identifying patterns or trends over time in the process control data. Analyzing trends provides valuable insights into whether variations are due to isolated incidents or if they indicate a systematic problem in the manufacturing process. For instance, observing a consistent increase in defect rates over several batches may signal an underlying issue that requires immediate attention.
Consider baking a cake where each batch turns out slightly different—sometimes too dry, sometimes too moist. Upon examining your oven temperature, you realize that it's fluctuating more than it should, resulting in inconsistent baking. This trend analysis helps pinpoint the core issue, just as it does in manufacturing processes.
Predictive Modeling
Predictive modeling uses historical process control data to forecast future outcomes. It involves leveraging data-driven techniques to anticipate potential deviations in the manufacturing process. By identifying early warning signs through predictive modeling, organizations can proactively address issues before they escalate, mitigating production disruptions and quality concerns.
Think of predictive modeling as using weather predictions to prepare for a storm. By forecasting potential changes based on historical data, you can take necessary precautions to avoid unwanted consequences.
Implementing these analysis techniques empowers organizations to make informed decisions and drive continuous improvements in their manufacturing processes, ultimately enhancing product quality and operational efficiency.
Incorporating these analysis methods into manufacturing processes not only boosts understanding but also ensures proactive management of potential issues, contributing to the overall efficiency and effectiveness of production systems.
Frequently Asked Questions about the Identification of SPC Out of Control Processes and Process Control Charts
What are the key indicators that a process is out of control?
Answer: The key indicators that a process is out of control include the presence of data points outside the control limits on a control chart, significant shifts or trends in the data, and patterns such as runs or cycles. These indicators suggest that the process is exhibiting variations beyond what would be expected due to chance alone. Statistical analysis can further support these indicators by calculating process capability indices, such as Cp and Cpk, which determine how well the process meets specifications and whether it is under control or not.
How can an organization interpret the data from an SPC out of control process control chart to improve their processes?
Answer: When an organization identifies an out of control process through a statistical process control (SPC) chart, it provides them with valuable insights to improve their processes. By understanding the specific cause of the variation, organizations can take corrective actions and make necessary adjustments to bring the process back under control. This can enhance product quality, reduce defects, decrease waste, and increase overall efficiency. For example, if a chart indicates an increase in defects above the control limits, organizations can investigate the root causes, such as equipment malfunction or operator errors, and address them accordingly.
How can an SPC out of control process control chart help in identifying variations in a process?
Answer: A Statistical Process Control (SPC) out of control chart can help in identifying variations in a process by visually highlighting when the process is operating outside of its normal range. By plotting process data on the control chart, any points that fall beyond the control limits indicate potentially significant variations. This helps identify when a process is out of control and requires investigation to find the cause of the variation. Statistical analysis and calculations such as standard deviations and control limits help in determining if the observed variations are statistically significant or merely random noise.
What are the benefits of using an SPC out of control process control chart in quality management?
Answer: Using an SPC out of control process control chart in quality management offers several benefits. Firstly, it provides a visual representation of process performance, making it easier to identify and address issues. Secondly, it helps in distinguishing between common cause and special cause variations, enabling appropriate action to be taken. Research shows that organizations implementing SPC techniques experience a significant reduction in defects, with one study reporting a 45% decrease in defect rates after implementation (source: "Implementing Statistical Process Control to Improve Quality Performance" by A. K. Memon et al., 2018). Additionally, SPC charts promote a proactive approach by highlighting trends and patterns early on, allowing for timely interventions and continuous improvement efforts.
Are there any specific industries or sectors where SPC out of control charts are commonly used?
Answer: Yes, SPC out of control charts are commonly used in industries such as manufacturing, healthcare, and software development. In manufacturing, SPC charts help identify variations in product quality and ensure consistent production. For example, a study conducted by Rana et al. (2017) found that implementing SPC charts resulted in a 16.4% reduction in defects within a manufacturing company. Similarly, in healthcare, SPC charts assist in monitoring patient outcomes and improving care processes. Additionally, software development teams use SPC charts to track code quality and identify programming errors. Overall, these industries rely on SPC out of control charts to proactively manage process variations and enhance overall performance.
What are the indicators of an out of control process?
Answer: Indicators of an out-of-control process are typically revealed through Control Charts, where points falling outside control limits, non-random patterns, or trends signify instability. Sudden shifts, excessive variation, or systematic patterns in the plotted data points are key indicators. These anomalies can signal potential issues within the process that require immediate attention. Regular monitoring and interpretation of these indicators allow for proactive identification and prompt corrective actions, ensuring the maintenance of a stable and controlled production environment.
What is Control Chart (Process Control Chart)?
Answer: A Control Chart, also known as a Process Control Chart, is a graphical tool used in statistical process control to monitor and visualize the stability and consistency of a process over time. It displays plotted data points, typically derived from samples taken at different time intervals, along with control limits that indicate the expected variation in the process. The chart helps identify trends, patterns, or outliers that may suggest the process is out of control. By providing a visual representation of process performance, control charts empower practitioners to detect and address variations promptly, thereby enhancing the overall quality and stability of the production or business process.
How do you ensure Process Control Chart precision and accuracy?
Answer: To ensure precision and accuracy in Process Control Charts, meticulous attention must be devoted to the selection and collection of representative samples from the process. Thoroughly understanding the process and its inherent variability is crucial. Employing statistical methods and tools helps in accurately calculating control limits and identifying any potential sources of variation. Regular monitoring and updating of the control chart are essential to reflect any changes in the process over time. Additionally, adherence to standardized procedures and consistency in data collection contribute to the reliability of the chart, ultimately enhancing its precision and accuracy in depicting the true state of the monitored process.
What are the benefits of using SPC in quality management?
Answer: The implementation of Statistical Process Control (SPC) in quality management provides a myriad of benefits. Firstly, SPC enables real-time monitoring of processes, allowing for early detection of deviations and potential issues. This proactive approach minimizes defects, reduces waste, and enhances overall product quality. Additionally, SPC facilitates data-driven decision-making by offering insights into process variation, empowering organizations to make informed adjustments and improvements. The use of control charts in SPC visually represents process performance over time, aiding in trend analysis and helping teams identify areas for optimization. Ultimately, SPC fosters continuous improvement, ensuring consistent and high-quality outcomes in various industries.
What does it mean when an SPC (Statistical Process Control) chart is out of control?
Answer: When an SPC chart is out of control, it signifies that the process being monitored is exhibiting variations beyond what is considered normal or expected. The chart, which typically displays data points over time, shows points or patterns that deviate from the expected statistical behavior. This deviation could be caused by various factors such as external influences, equipment malfunctions, or changes in the process itself. Identifying and addressing these out-of-control signals is crucial in maintaining the stability and quality of the monitored process, as it helps prevent defects and ensures that the production stays within specified limits.
Recap for Out of Control Processes (SPC) Identified by Control Charts
In summary, the identification of out-of-control processes through Statistical Process Control (SPC) charts is an integral aspect of quality management. By utilizing control charts, organizations gain a visual representation of process variation over time, enabling them to discern patterns and anomalies. Recognizing when a process deviates from its expected statistical behavior empowers decision-makers to intervene promptly, addressing the root causes of instability and preventing the escalation of defects or errors in the final output.
It is paramount for organizations to view the management of out-of-control processes as an opportunity for continuous improvement. Implementing corrective actions based on the insights gained from SPC charts not only restores process stability but also contributes to long-term efficiency and product quality. Regularly monitoring and analyzing control charts should be an ongoing practice embedded in the organizational culture, fostering a proactive approach to quality assurance.
>
As a further resource for those keen on enhancing their understanding of quality management methodologies, we encourage readers to
Request a free of charge copy of the Six Sigma Framework book. This comprehensive guide delves into the principles and techniques of Six Sigma, providing valuable insights into process improvement, variability reduction, and overall excellence in organizational performance. Embracing the principles outlined in the Six Sigma Framework can significantly contribute to the successful identification and management of out-of-control processes, ultimately fostering a culture of continuous improvement within your organization.